Corrugated Industry
Modern corrugated box production
Equipped for the future
The demands imposed on corrugated transport packaging are on the rise. Customers expect their products to be fully protected and to reach consumers undamaged. For you as a manufacturer, these demands pose new challenges every day in production and product development. This is where a reliable partner for adhesive application comes in. Our latest technologies give you a technology lead, and promote your success with sustainable products.
Your applications Our solutions
Baumer hhs is your partner
Our systems can be adapted to your individual needs. Benefit from our technology lead and Baumer hhs’s reputation for reliability.
Modular design for configuring complete gluing systems
OEM supplier to leading, global packaging machine manufacturers
Future-oriented and cost-efficient
For sustainable production processes
Everything you need from a single supplier
We help prepare your team for the future
We offer you support for your applications
Zero-waste – Products that pay off
The Xtend³ system controls and monitors your production process.
A closed-loop system for the non-contact gluing of corrugated flaps, it minimises cleaning and setup times, avoids waste and is absolutely reliable at maximum speed. Get the benefit of our experience – also for complex products. A complete system from a single supplier.
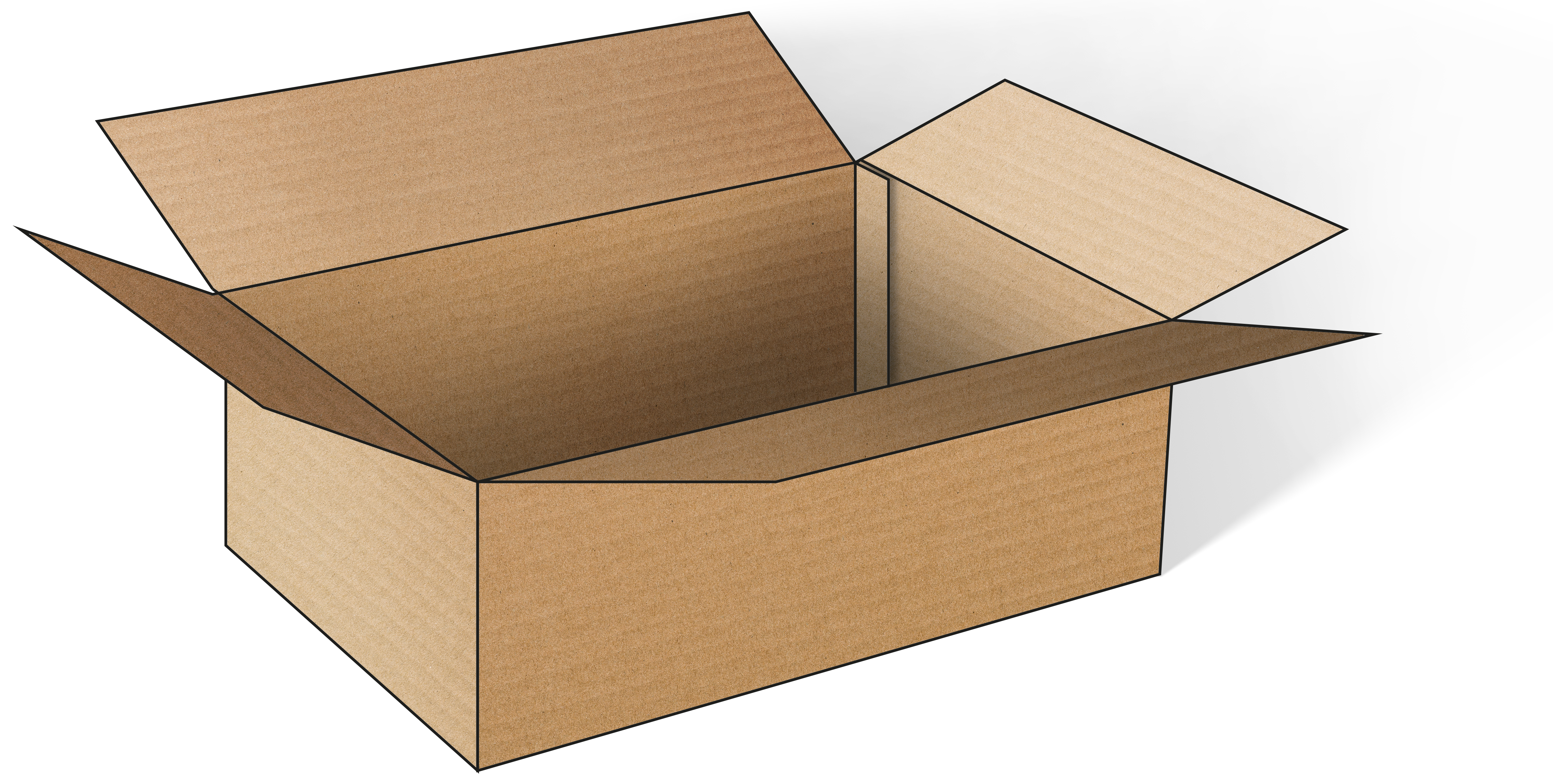
Integrated water bath
- The Baumer hhs cold glue heads are “parked” in a water bath when at rest or during interruptions in production.
- Protects against drying out, glue issues and contamination.
- When starting or re-starting production, the multi-application head automatically travels into the specified position.
- Glue is applied perfectly from the first product on.
Optimum amount of adhesive
- Piston pumps with pressure regulators adapt the adhesive pressure, and in turn the amount of glue applied, to the machine speed.
- The glue feed can be adapted to your requirements.
- Adhesive can be conveyed as needed either from a container or directly via a supply line.
Reliability thanks to monitoring with the PGD 1000
- Reliably detects defective products.
- Sensor reliably detects adhesives even without added optical brighteners or colourants.
- Capable of monitoring several glue tracks.
Be flexible with Inverto.
- Non-contact gluing of inner and outer flaps.
- System setup can be changed quickly and easily.
- Just a few manual adjustments is all it takes to change the setup of the Inverto, increasing your flexibility.
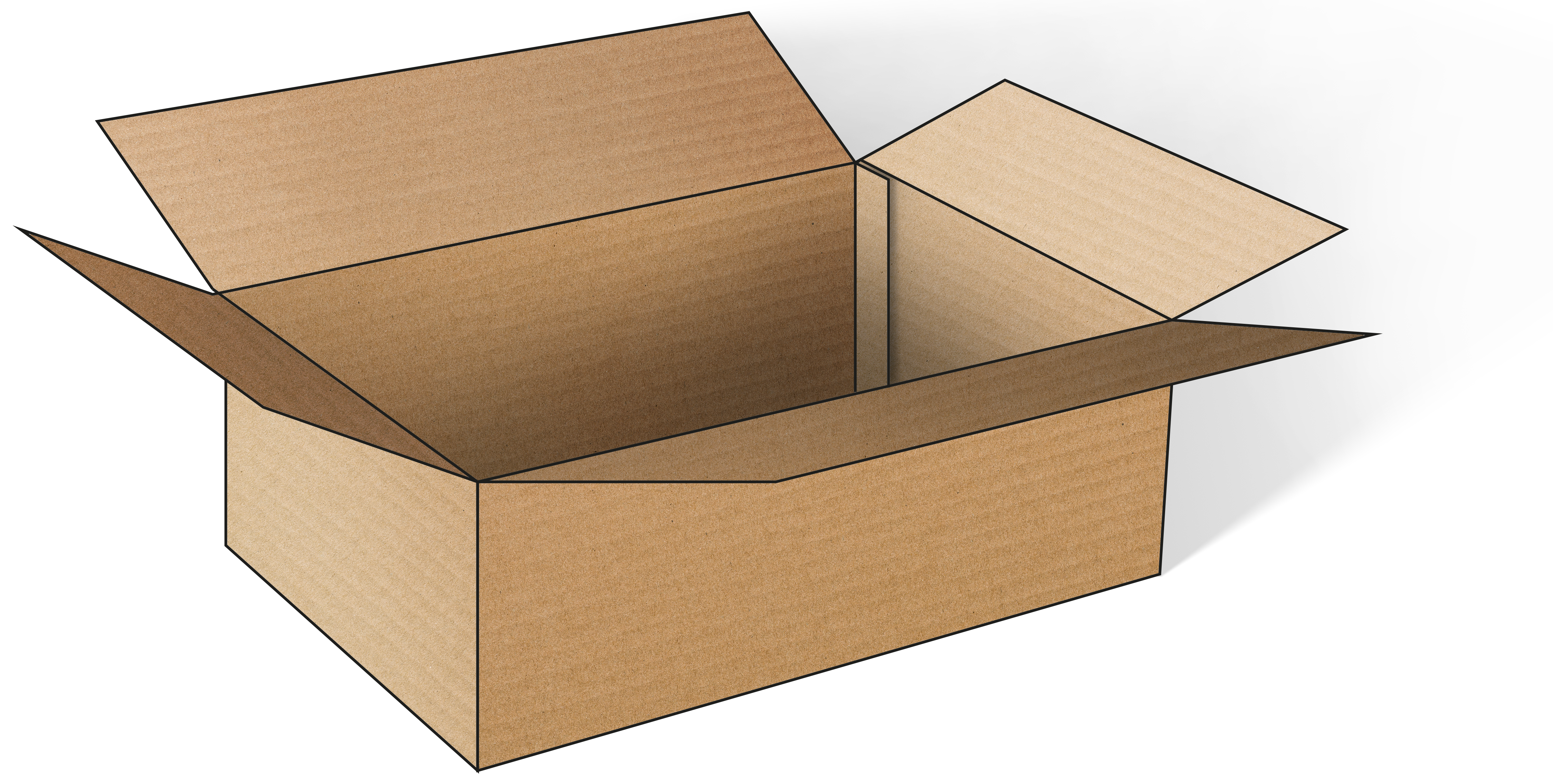
Integrated water bath
- The Baumer hhs cold glue heads are “parked” in a water bath when at rest or during interruptions in production.
- Protects against drying out, glue issues and contamination.
- When starting or re-starting production, the multi-application head automatically travels into the specified position.
- Glue is applied perfectly from the first product on.
Optimum amount of adhesive
- Piston pumps with pressure regulators adapt the adhesive pressure, and in turn the amount of glue applied, to the machine speed.
- The glue feed can be adapted to your requirements.
- Adhesive can be conveyed as needed either from a container or directly via a supply line.
Reliability thanks to monitoring with the PGD 1000
- Reliably detects defective products.
- Sensor reliably detects adhesives even without added optical brighteners or colourants.
- Capable of monitoring several glue tracks.
Be flexible with Inverto.
- Non-contact gluing of inner and outer flaps.
- System setup can be changed quickly and easily.
- Just a few manual adjustments is all it takes to change the setup of the Inverto, increasing your flexibility.
Zur Anzeige des Klick-Modells nutzen Sie gerne unsere Desktop-Version.
Box Monitoring – Detecting deviations quickly and easily
As a corrugated board manufacturer, you face steadily rising demands on production speed and quality. Manual intervention in a running production process slows it down significantly. Automated quality assurance methods are the key to your success in this case. Check, eject, document – the Box Monitoring systems from Baumer hhs do it all.
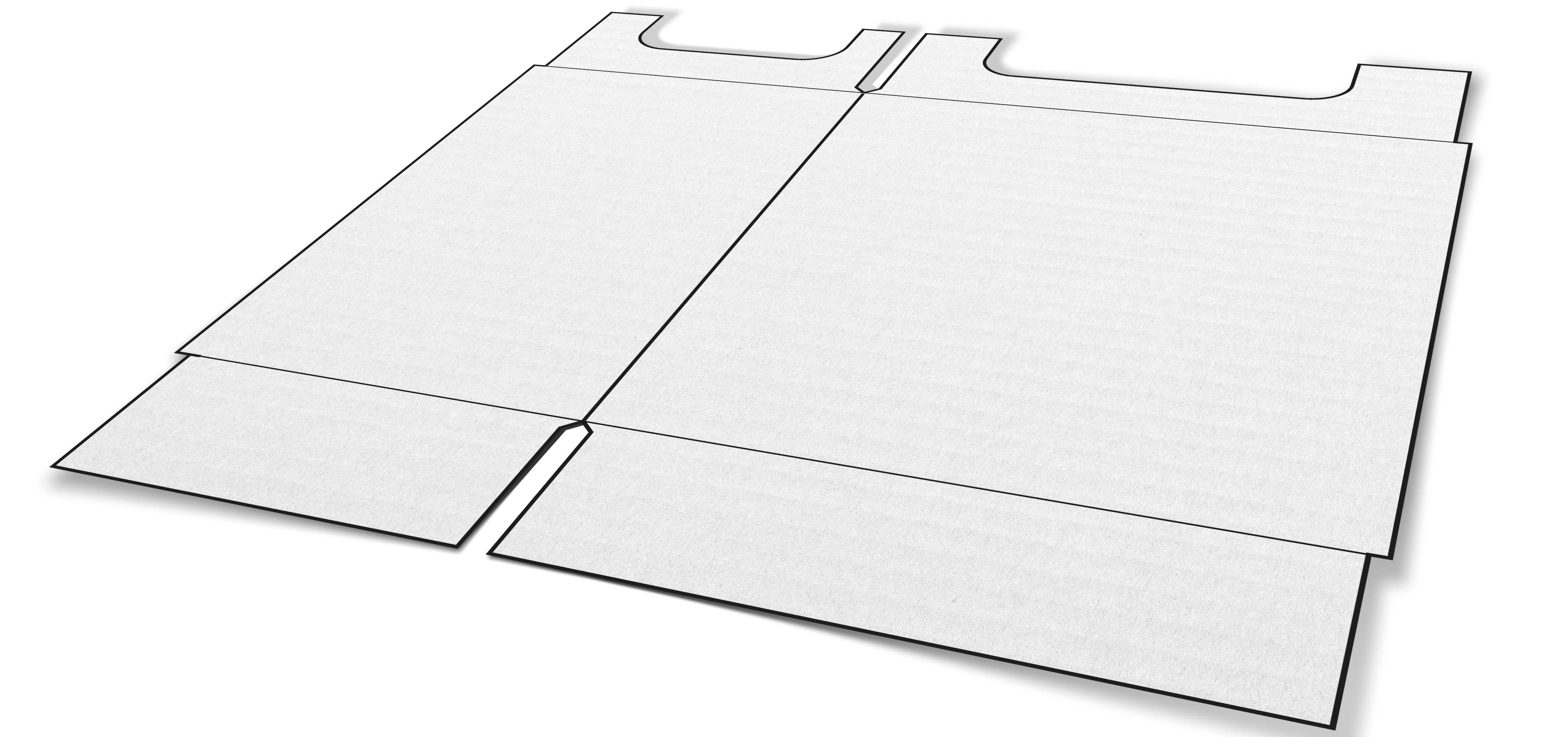
Reliably measuring and evaluating gaps
- The system reliably checks the position of glued blanks.
- The GAP control system is based on a patented method that combines a high-resolution sensor with a laser beam, making it considerably superior to simple camera systems.
- No matter whether boxes are printed or unprinted, the system measures the front and rear gaps with millimetre accuracy.
Ensuring quality printing
- Register control checks that up to six different inks are positioned correctly relative to one another.
- The first printed ink serves as the reference.
- After a teaching cycle with ten sheets, the reference value is entered in the system.
- Any deviations are then detected quickly and easily (measuring accuracy/repeat accuracy +/- < 0.05 mm).
Checking slot position and quality
- Slot depth is measured by sensor.
- System detects if slots have shifted, or if no punched slots exist at all.
- Also detects any fragments left behind in a slot from the punching process.
- The Xtend³ controller keeps you informed at all times.
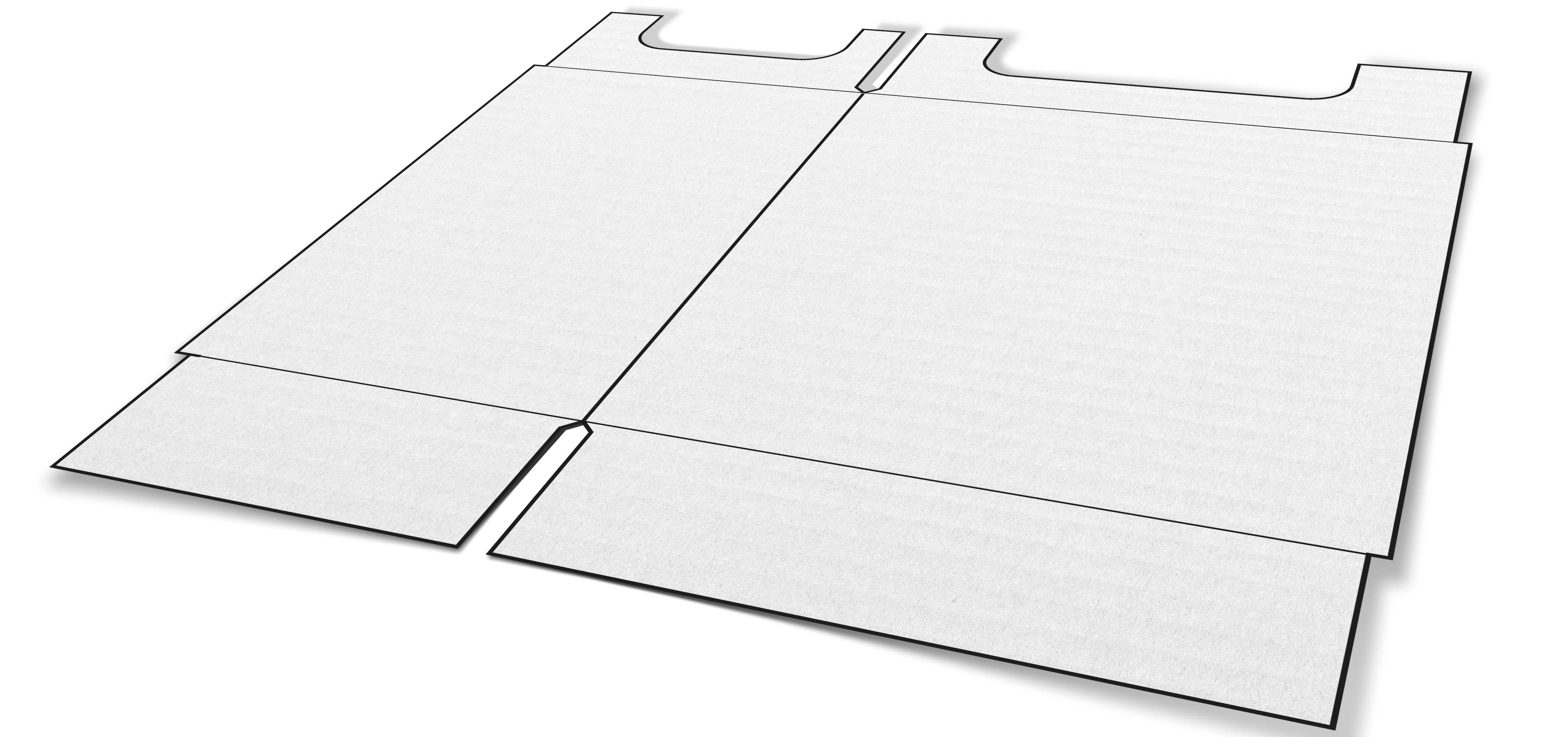
Reliably measuring and evaluating gaps
- The system reliably checks the position of glued blanks.
- The GAP control system is based on a patented method that combines a high-resolution sensor with a laser beam, making it considerably superior to simple camera systems.
- No matter whether boxes are printed or unprinted, the system measures the front and rear gaps with millimetre accuracy.
Ensuring quality printing
- Register control checks that up to six different inks are positioned correctly relative to one another.
- The first printed ink serves as the reference.
- After a teaching cycle with ten sheets, the reference value is entered in the system.
- Any deviations are then detected quickly and easily (measuring accuracy/repeat accuracy +/- < 0.05 mm).
Checking slot position and quality
- Slot depth is measured by sensor.
- System detects if slots have shifted, or if no punched slots exist at all.
- Also detects any fragments left behind in a slot from the punching process.
- The Xtend³ controller keeps you informed at all times.
Zur Anzeige des Klick-Modells nutzen Sie gerne unsere Desktop-Version.
CorrBox Solution
The packaging industry is under pressure on all sides to make changes. For you as a manufacturer, this means facing new challenges every day in production and product development.
Our CorrBox Solution meets tomorrow’s demands in the industry today!
CorrBox Solution is a complete modular system. You can upgrade your system on every time, when your demands are growing.
Take a look at our CorrBox-Webinar
All benefits and the complete solution is explained in our customer webinar.
CorrBox Solution
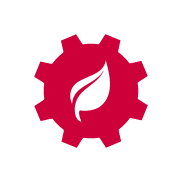
Sustainability
Resource-efficient for increased sustainability
Fast setup with less waste
Water bath ensures perfect application quality from the very first product on
Quality assurance and product tracking reduce production waste
Glue save mode reduces adhesive consumption
Glue monitoring requires no optical brighteners or UV tracers
Developed for greater reliability in production
Fail-safe principle
100% quality control
Perfect adhesive application
Water bath for perfect restart
Production data networking and analysis

Reliability