
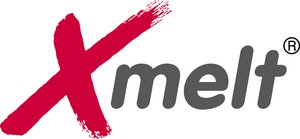
Baumer hhs offers everything for the application and processing of hot melt adhesives. The systems and components are used in many industrial applications.
From energy-efficient melters to long-life electrical application heads, Baumer hhs is your one-stop partner.
Xmelt Melting devices
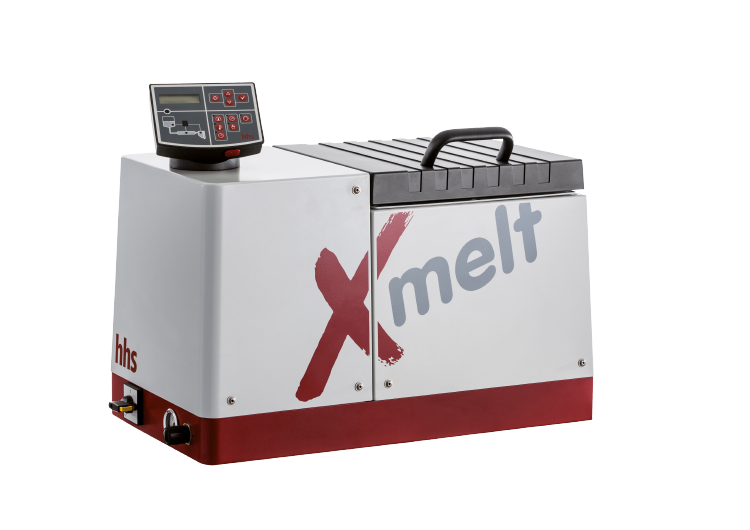
Saves energy and protects the adhesive
The Xmelt melters have been developed for a variety of applications in different industries. The efficient units feature low energy consumption, helping to minimise the CO2 emissions of your production.
- Two-zone tank
- Up to 6 hose connections
- Bus connection
- Capacitive level monitoring
- Auto ECO Mode
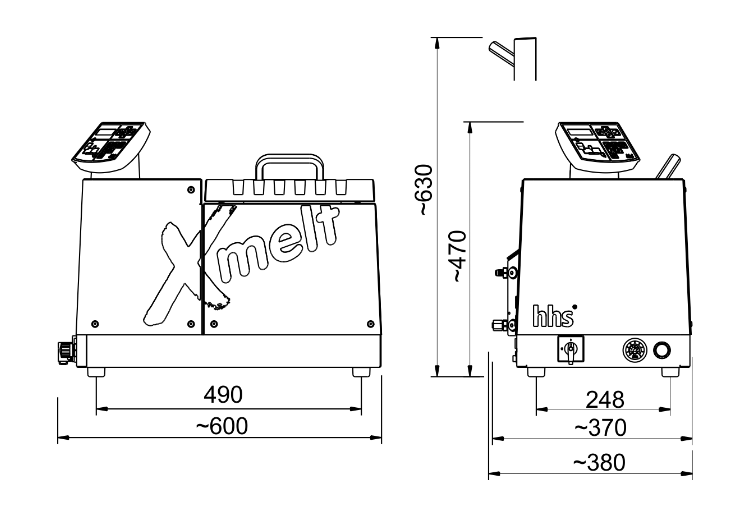
Technical Data
Specification | Value | Unit |
---|---|---|
Temperature range | 20-200 | °C |
Control accuracy | ± 0,5 | °C |
Degree of protection | IP40 | |
Noise level | <70 | dB |
Heating time | 20 | min |
Heating capacity tank, 3/N/PE AC | 2,1 | kW |
Heating capacity tank, 3/PE AC | 1,46 | kW |
Rated current tank, 3/N/PE AC | 4,59 | A |
Rated current tank, 3/PE AC | 3,83 | A |
Tank capacity | 4 | kg |
Melt capacity | 8 | kg/h |
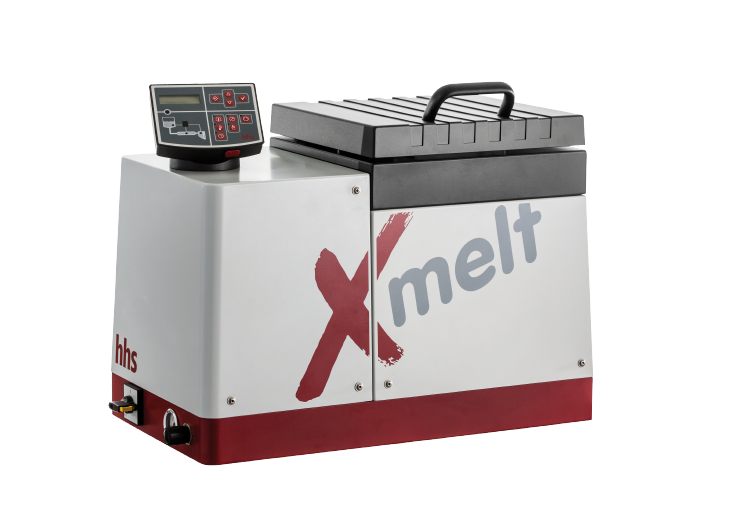
Saves energy and protects the adhesive
The Xmelt melters have been developed for a wide range of applications in various industries. The efficient units are characterised by low energy consumption and thus help to minimise the CO2 emissions of your production.
- Two zone tank
- Up to 8 hose connections
- Bus connection
- Capacitive level monitoring
- Auto ECO Mode
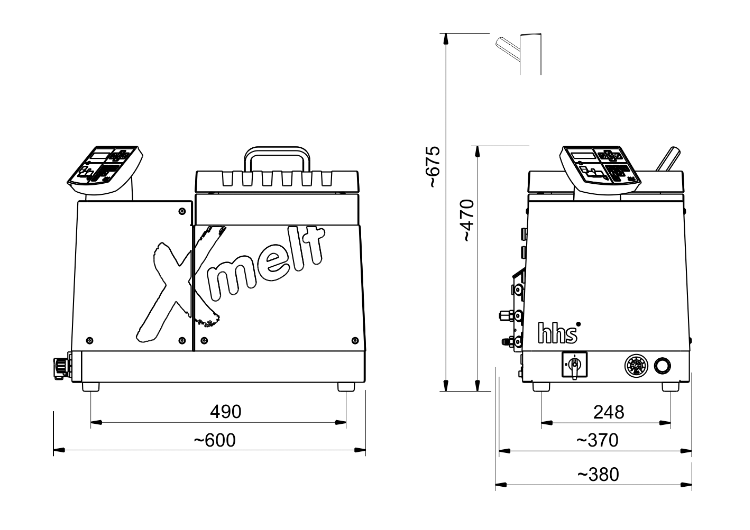
Technical Data
Specification | Value | Unit |
---|---|---|
Temperature range | 20-200 | °C |
Control accuracy | ± 0,5 | °C |
Degree of protection | IP40 | |
Noise level | <70 | dB |
Heating time | 20 | min |
Heating capacity tank, 3/N/PE AC | 2,63 | kW |
Heating capacity tank, 3/PE AC | 1,83 | kW |
Rated current tank, 3/N/PE AC | 5,74 | A |
Rated current tank, 3/PE AC | 4,80 | A |
Tank capacity | 8 | kg |
Melt capacity | 10 | kg/h |
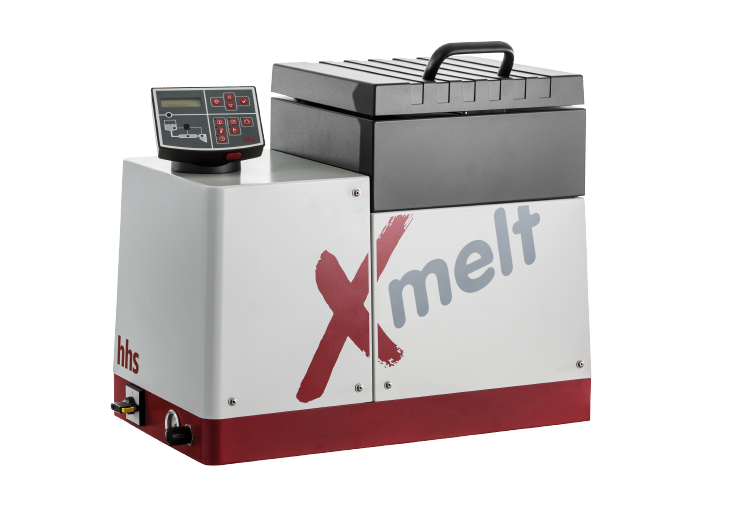
Saves energy and protects the adhesive
The Xmelt melters have been developed for a wide range of applications in various industries. The efficient units are characterised by low energy consumption and thus help to minimise the CO2 emissions of your production.
- Two zone tank
- Up to 8 hose connections
- Bus connection
- Capacitive level monitoring
- Auto ECO Mode
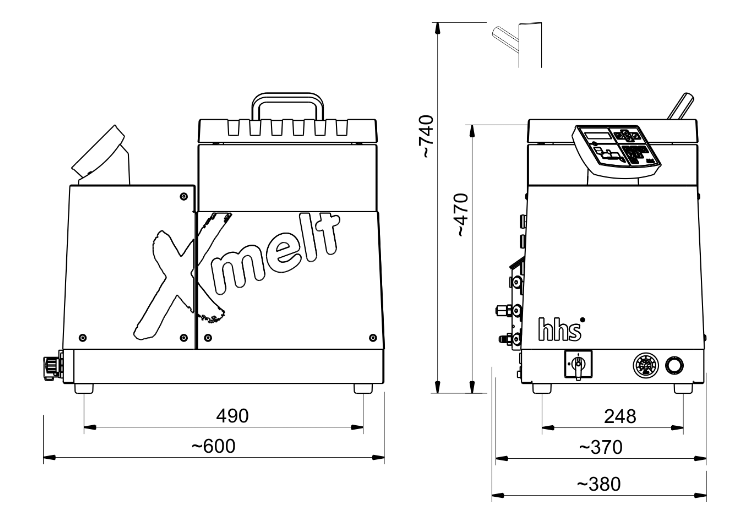
Technical Data
Specification | Value | Unit |
---|---|---|
Temperature range | 20-200 | °C |
Control accuracy | ± 0,5 | °C |
Degree of protection | IP40 | |
Noise level | <70 | dB |
Heating time | 19 | min |
Heating capacity tank, 3/N/PE AC | 2,9 | kW |
Heating capacity tank, 3/PE AC | 2,2 | kW |
Rated current tank, 3/N/PE AC | 6,61 | A |
Rated current tank, 3/PE AC | 5,75 | A |
Tank capacity | 12 | kg |
Melt capcity | 11,2 | kg/h |
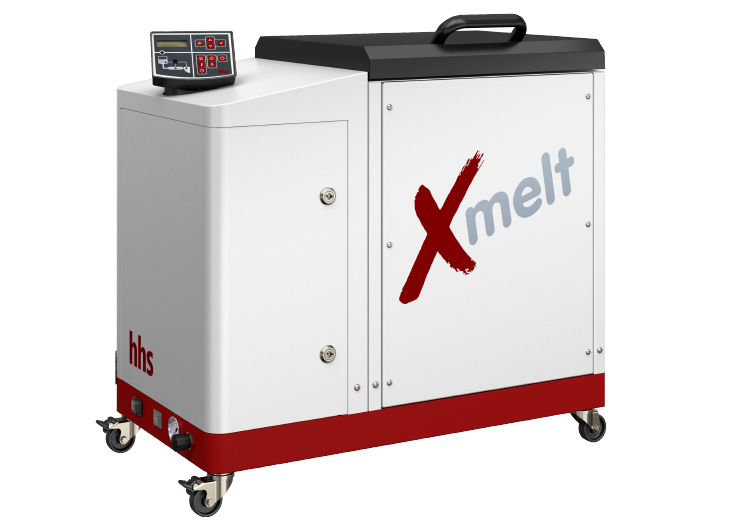
Saves energy and protects the adhesive
The Xmelt melters have been developed for a wide range of applications in various industries. The efficient units are characterised by low energy consumption and thus help to minimise the CO2 emissions of your production.
- Two zone tank
- Up to 8 hose connections
- Bus connection
- Capacitive level monitoring
- Auto ECO Mode
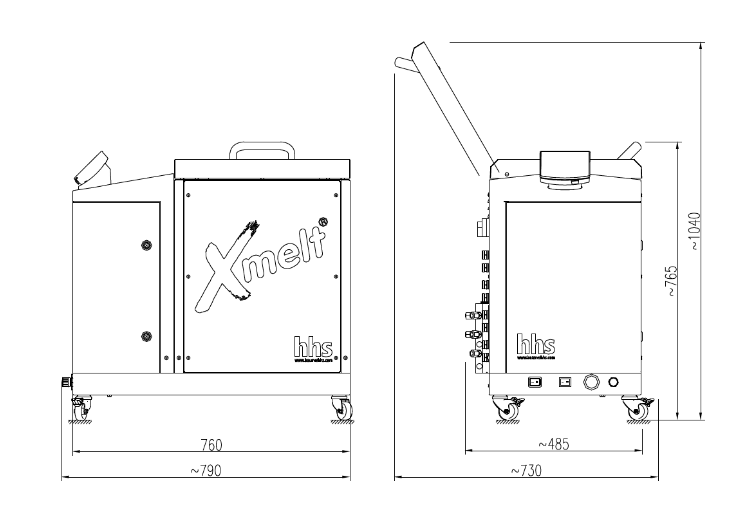
Technical Data
Specification | Value | Unit |
---|---|---|
Temperature range | 20-200 | °C |
Control accuracy | ± 1 | °C |
Degree of protection | IP40 | |
Noise level | <70 | dB |
Heating time | 25 | min |
Heating capacity tank | 4 | kW |
Rated current tank | 10,3 | A |
Tank capacity | 25 | kg |
Melting capacity (depending on adhesive) | 25 | kg/h |
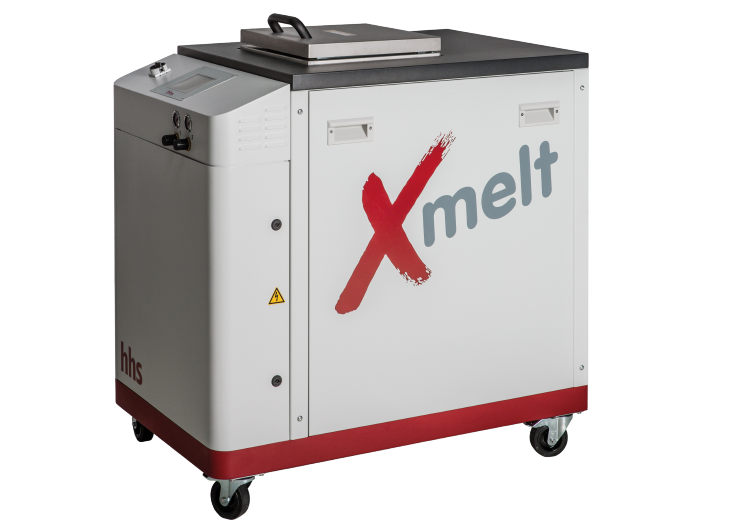
Designed for e-commerce
The Xmelt melters are designed for a wide range of industrial applications. The efficient units with their high melting rate are suitable for the production of e-commerce boxes made of corrugated board.
- Two zone tank
- Up to 2 hose connections
- One or two piston pumps
- Capacitive level monitoring
- Auto ECO Mode
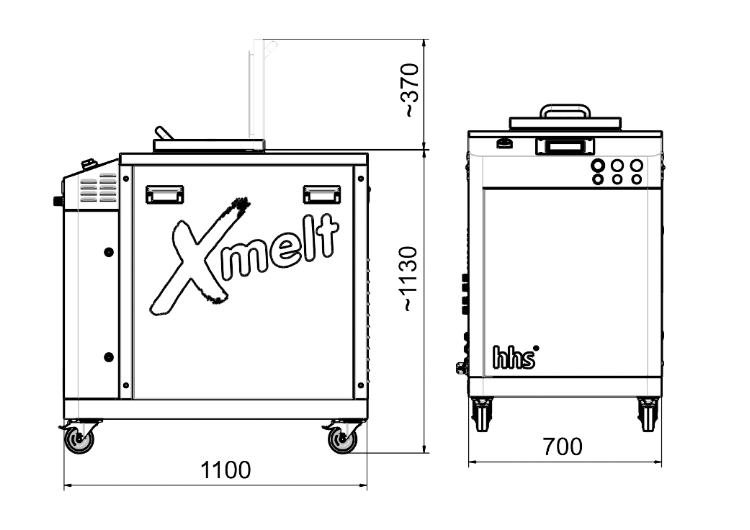
Technical Data
Specification | Value | Unit |
---|---|---|
Temperature range | 20-200 | °C |
Control accuracy | ± 1 | °C |
Degree of protection | IP40 | |
Noise level | <70 | dB |
Heating time | 30 | min |
Heating capacity | 2,9 | kW |
Material pressure | 80 | bar |
Tank capacity | 100 | kg |
Melt capacity (depending on adhesives) | 100 | kg/h |
Xmelt Heated hoses
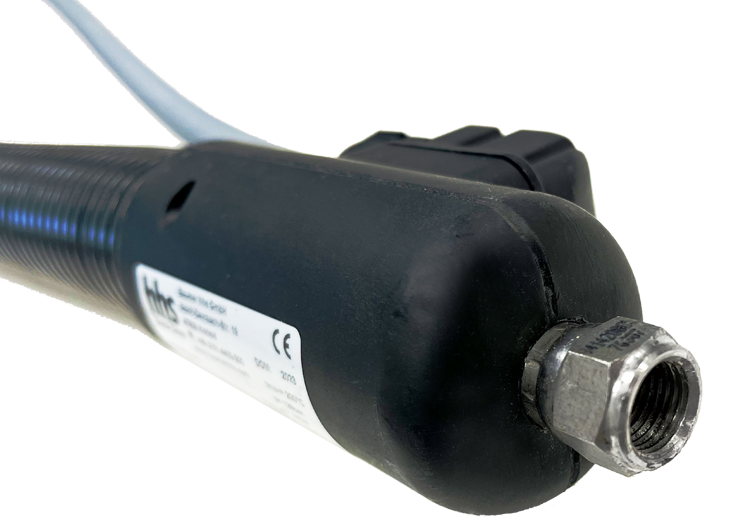
Innovative solution prevents charing!
The new DF hoses (degradation free) are developed to get the highest productivity in hot melt applications.
With a special designed metal inner core the DF hoses prevent degradation of hot melt inside the hose for days. No charing means no blocked nozzles and filters.
- Eliminates charing
- Clogged nozzles and filters are a thing of the past
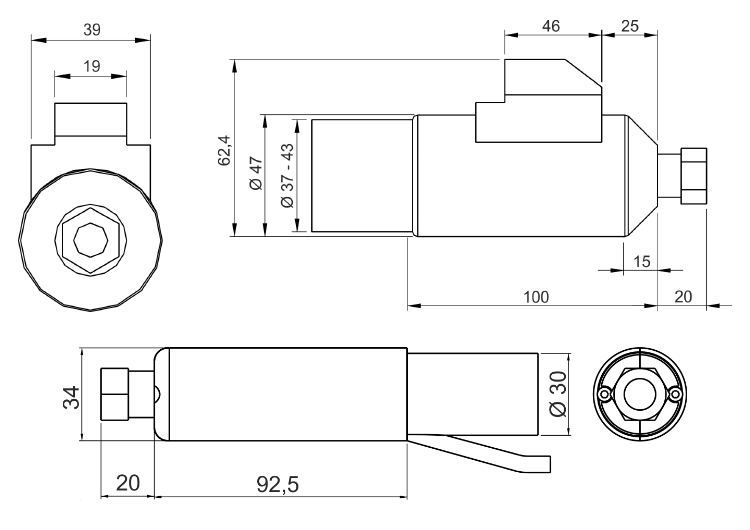
Technical data
Specification | Value | Unit |
---|---|---|
Operating voltage | 1N~230 ± 10% | V |
Temperature sensor | PT 100 | |
Connected load | 130 | W/m |
Degree of protection | IP54 | |
Maximum operating temperature | 200 | °C |
Maximum operating pressure | 90 | bar |
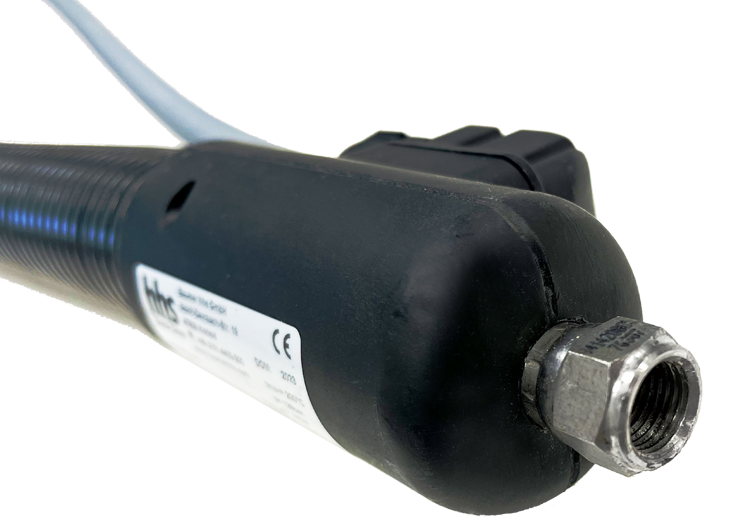
Innovative solution prevents charing!
The new DF hoses (degradation free) are developed to get the highest productivity in hot melt applications.
With a special designed metal inner core the DF hoses prevent degradation of hot melt inside the hose for days. No charing means no blocked nozzles and filters.
Eliminates charing
Clogged nozzles and filters are a thing of the past
Compatible for Nordson* Series 2300/3000 and ProBlue Series*
*Nordson and ProBlue are registered trademarks of Nordson Corporation
Technical data
Specification | Value | Unit |
---|---|---|
Operating voltage | 1N~230 ± 10% | V |
Temperature sensor | Ni120 | |
Connected load | 110 | W/m |
Degree of protection | IP54 | |
Maximum operating temperature | 200 | °C |
Maximum operating pressure | 120 | bar |
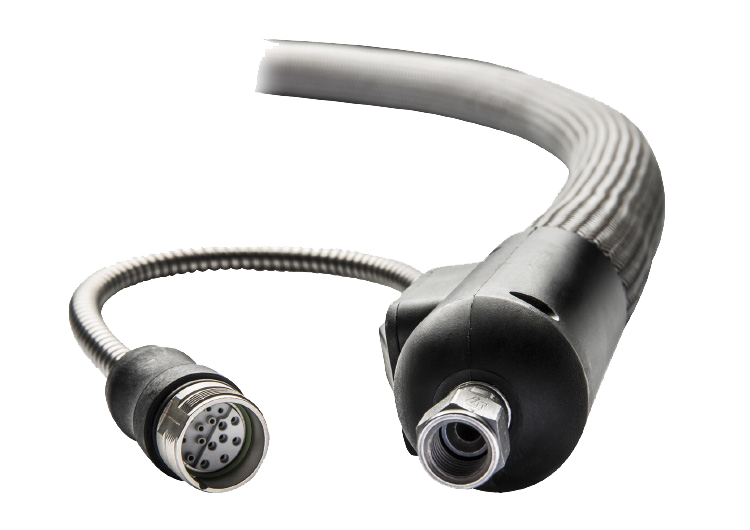
Safety for production and employees
The heated hot melt hoses from Baumer hhs are available in many lengths and are perfectly adapted to your application. The insulated hoses ensure a constant temperature control for maximum production safety and protects the personnel from burns.
- Suitable for the tightest of spaces
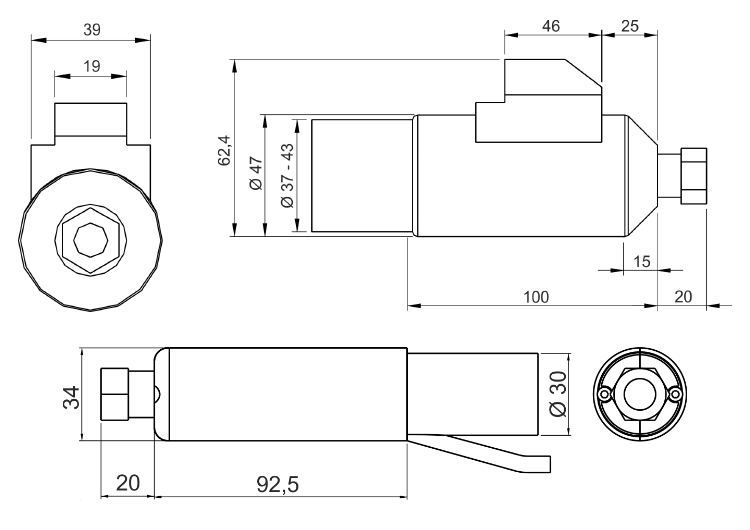
Technical data
Specification | Value | Unit |
---|---|---|
Operating voltage | 1N~230 ± 10% | V |
Temperature sensor | PT 100 | |
Connected load | 130 | W/m |
Degree of protection | IP40 | |
Maximum operating temperature | 200 | °C |
Maximum operating pressure | 90 | bar |
Outer diameter | 45 mm und 30 mm |
Adhesives: EVA, PE, PO APAO, PA, PSA, PUR, Fugitive, Remoist
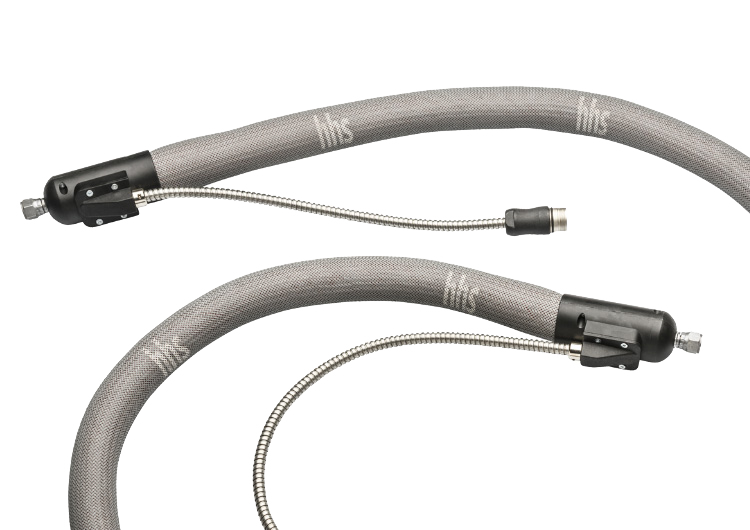
The plus in safety
Increase the safety in your production. The hot melt hoses of the AL series from Baumer hhs all have an integrated overheating switch.
Safety that lets you sleep peacefully.

Technical data
Specification | Value | Unit |
---|---|---|
Operating voltage | 1N~230 ± 10% | V |
Temperature sensor | PT 100 | |
Connected load | 130 | W/m |
Degree of protection | IP54 | |
Maximum operating temperature | 200 | °C |
Maximum operating pressure | 90 | bar |
Adhesives: EVA, PE, PO APAO, PA, PSA, PUR, Fugitive, Remoist
Xmelt Application heads - Electromagnetic
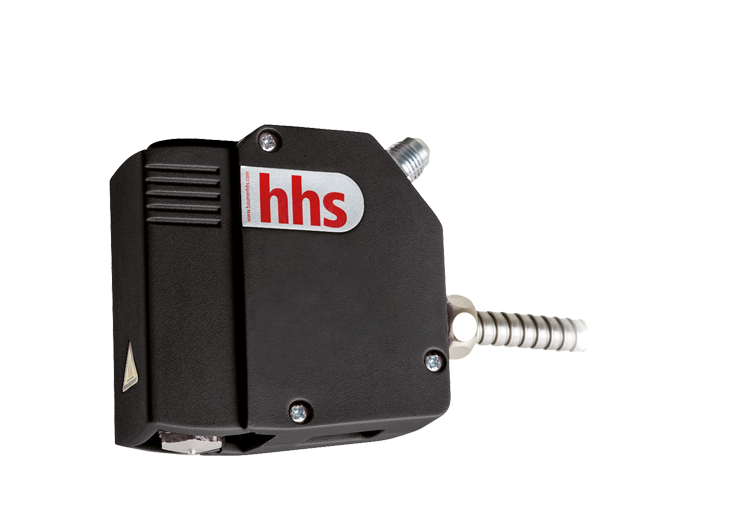
The precision of electric. Powerful like pneumatics!
Baumer hhs’s new PXH 1000 is an electric hot melt applicator that raises the bar in industrial gluing: high switching frequency, precision cut-off behaviour and maximum flexibility in selecting adhesives.
- Maximum availability with over 1 billion switching operations
- Short actuation times and 450 Hz application frequency
- Maximum safety due to integrated overtemperature switch
- Highest flexibility up to 7,000 mPa.s
- Closing force like pneumatic applicators
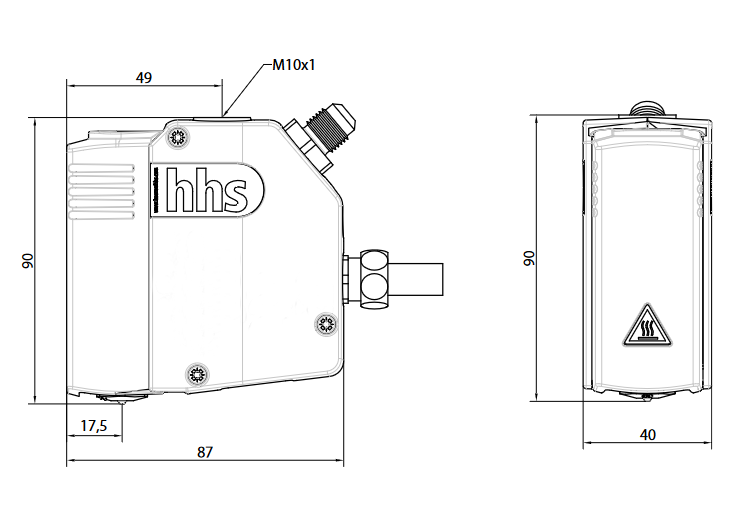
Technical data
Specification | Value | Unit |
---|---|---|
Temperature range | 0-200 | °C |
Temperature monitoring | Pt 100 | |
Switching frequency | 450 | Hz |
Connection | 15 pole plug | |
Hose connection | 1/2" UNF | |
Adhesive pressure | 80 | bar |
Adhesive viscosity | max. 7.000 | mPa.s |
Noise emission | <70 | dB |
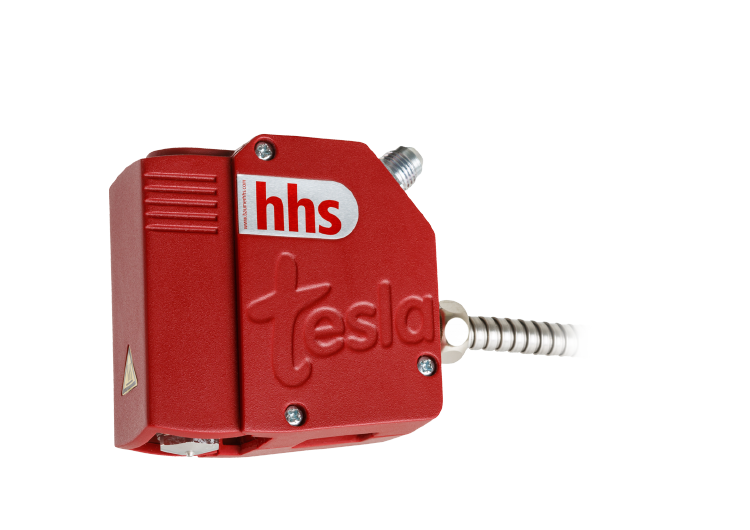
The hot melt head for the smallest dots at the highest machine speed
The tesla pro electromagnetic application head stands for maximum performance in packaging production. With its high availability and long service life, it helps to minimise production costs and make production more sustainable.
- Maximum availability with over 1 billion switching operations
- Short actuation times and 600 Hz application frequency
- Maximum safety due to integrated overtemperature switch
- Highest flexibility up to 5,000 mPa.s
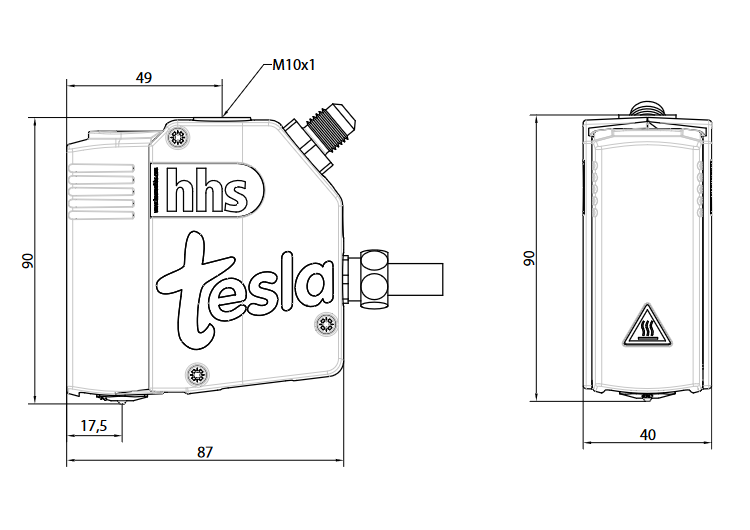
Technical data
Specification | Value | Unit |
---|---|---|
Temperature range | 0-200 | °C |
Temperature monitoring | Pt 100 | |
Switching frequency | 600 | Hz |
Connection | 15 pole plug | |
Hose connection | 1/2" UNF | |
Adhesive pressure | 80 | bar |
Adhesive viscosity | max. 5.000 | mPa.s |
Noise emission | 65 | dB |
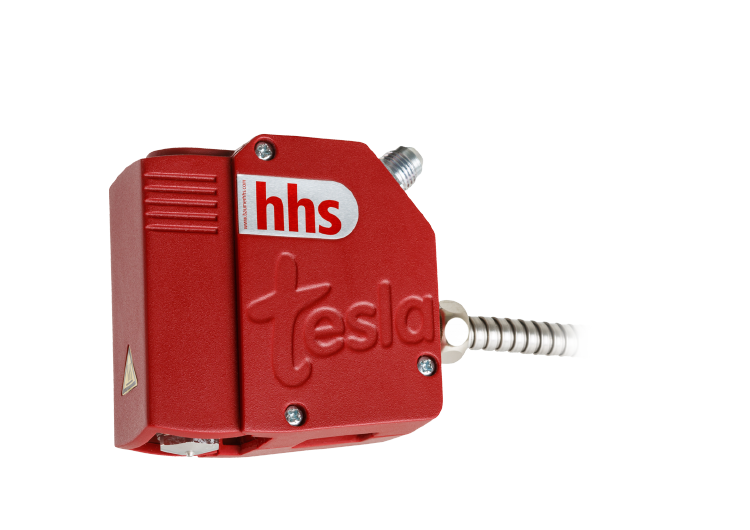
The innovative hot melt head controled via PLC 24V
The tesla evo provides the packaging industry with a powerful electromagnetic application head that can be controlled directly via the machine controller. The immense advantages of electromagnetic valves can now also be used in end-of-line packaging. This reduces production costs through adhesive savings and maximum availability of the packaging machines.
- Maximum availability with over 1 billion switching operations
- Simple control via SPS 24V
- Maximum safety due to integrated overtemperature switch
- Maximum flexibility up to 5,000 mPa.s
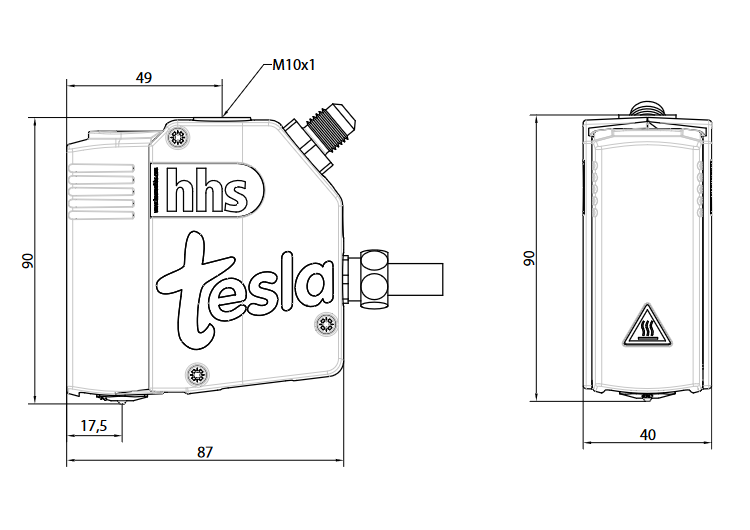
Technical data
Specification | Value | Unit |
---|---|---|
Temperature range | 0-200 | °C |
Temperature monitoring | Pt 100 | |
Switching frequency | 135 | Hz |
Connection | 15 pole plug | |
Hose connection | 1/2" UNF | |
Adhesive pressure | 80 | bar |
Adhesive viscosity | max. 5.000 | mPa.s |
Noise emission | 65 | dB |
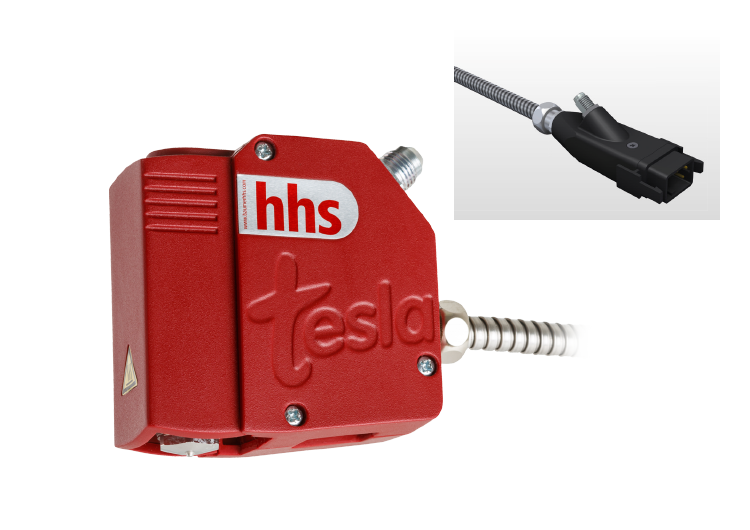
The innovative application head for use on third-party systems
The tesla go provides the packaging industry with a powerful electromagnetic application head that can be controlled directly via the machine controller. The immense advantages of electromagnetic valves can now also be used in end-of-line packaging. This reduces production costs through adhesive savings and maximum availability of the packaging machines.
- Maximum availability with over 1 billion switching operations
- Simple control via PLC 24V
- Maximum safety due to integrated excess temperature cut-off
- Maximum flexibility up to 5,000 mPa.s
- Easy integration due to competition-compatible connections
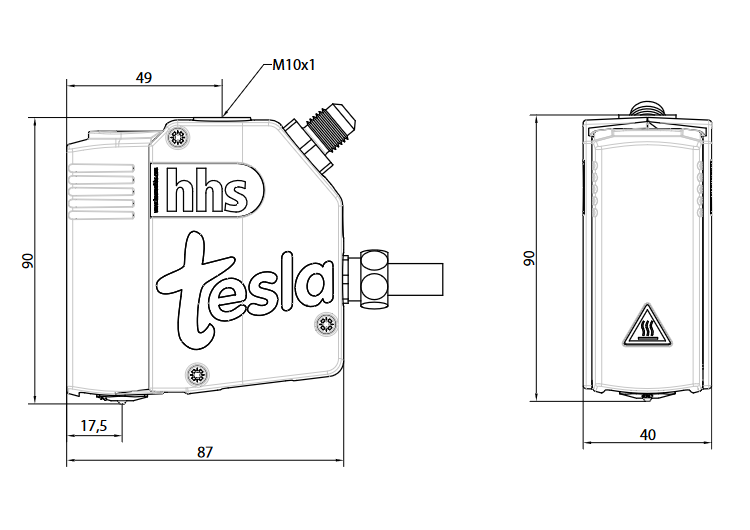
Technical data
Specification | Value | Unit |
---|---|---|
Temperature range | 0-200 | °C |
Temperature monitoring | Ni 120 | |
Switching frequency | 135 | Hz |
Connection | Stecker für den Betrieb an Fremdsystemen | |
Hose connection | 9/16-18 UNF | |
Adhesive pressure | 80 | bar |
Adhesive viscosity | 5.000 | mPa.s |
Noise emission | 65 | dB |
Xmelt Application heads - Electropneumatic
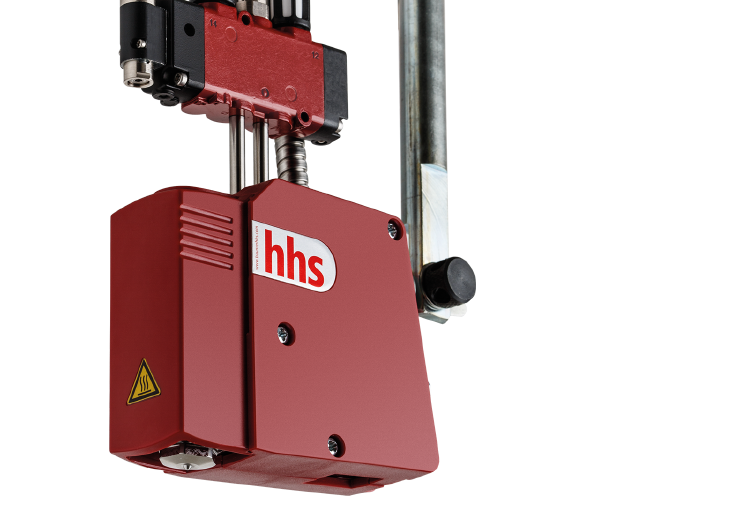
Electropneumatic head for bead and dot application
The aerto pro delivers maximum application quality, even with the most difficult adhesives. The powerful long-life module with innovative sealing technology convinces with perfect application at all speeds.
- Maximum flexibility in adhesive selection
- Long service life
- Perfect dot application
- Low maintenance costs
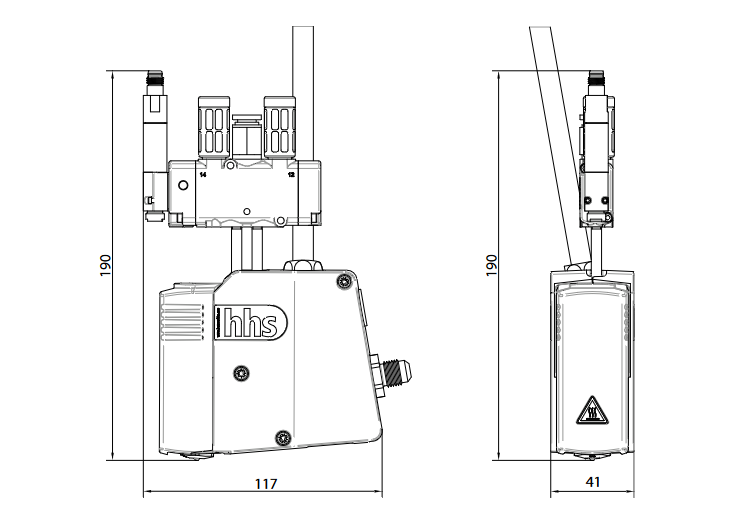
Technical data
Specification | Value | Unit |
---|---|---|
Temperature range | 0-200 | °C |
Temperature monitoring | Pt 100 | |
Switching frequency* | 350**/280 or 21.000**/16.000 | Hz |
Connection | 15 pole plug | |
Hose connection | 1/2“ UNF | |
Adhesive pressure | 80 | bar |
Adhesive viscosity | max. 60.000 | mPa.s |
Noise emission | 82 | dB*** |
* depending on nozzle size, adhesive and pressure** no continuous operation*** with sound insulation |
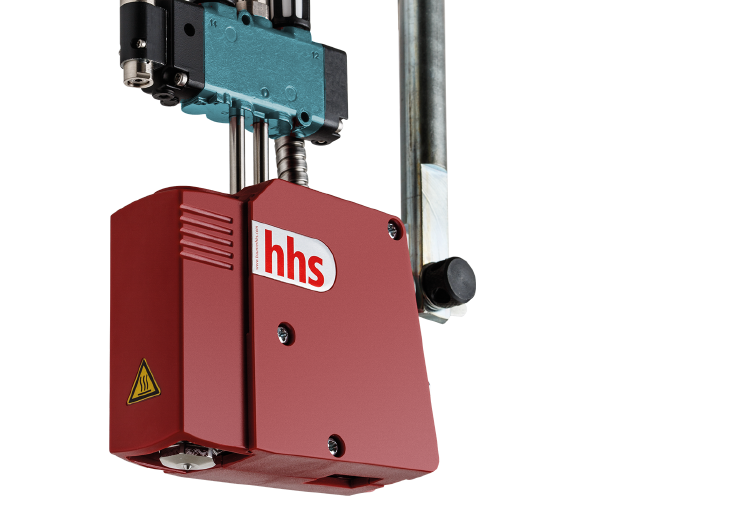
Powerhouse for end-of-line packaging
With the aerto evo, soiling of packaging machines due to thread pull and faulty gluing is history. The powerful head ensures clean application of dots and beads even in the most difficult installation situations. Safe and precise.
- Maximum safety with temperature cut-off
- Maximum flexibility in adhesive selection
- Simple control via SPS 24V
- Flexible for dot and line application
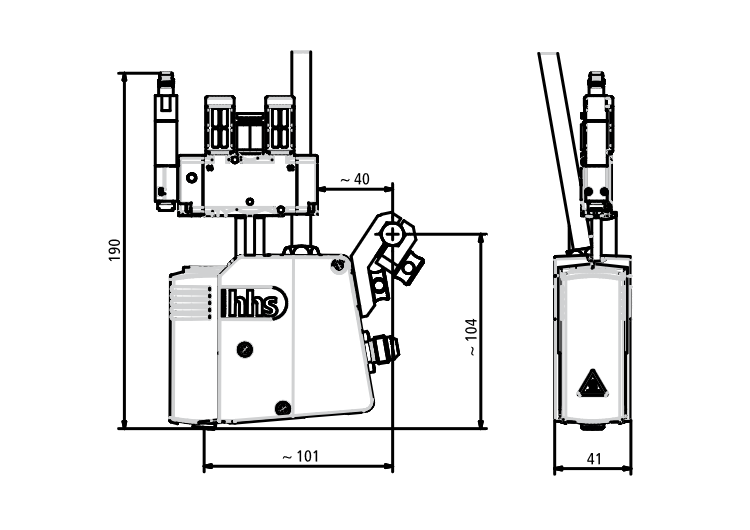
Technical data
Specification | Value | Unit |
---|---|---|
Temperature range | 0-200 | °C |
Temperature monitoring | Pt 100 | |
Switching frequency* | 250 | Hz |
Connection | 15 pole plug | |
Hose connection | 1/2“ UNF | |
Adhesive pressure | 80 | bar |
Adhesive viscosity | max. 60.000 | mPa.s |
Noise emission | 82 | db** |
* depending on nozzle size, adhesive and pressure ** no continuous operation*** with sound insulation |
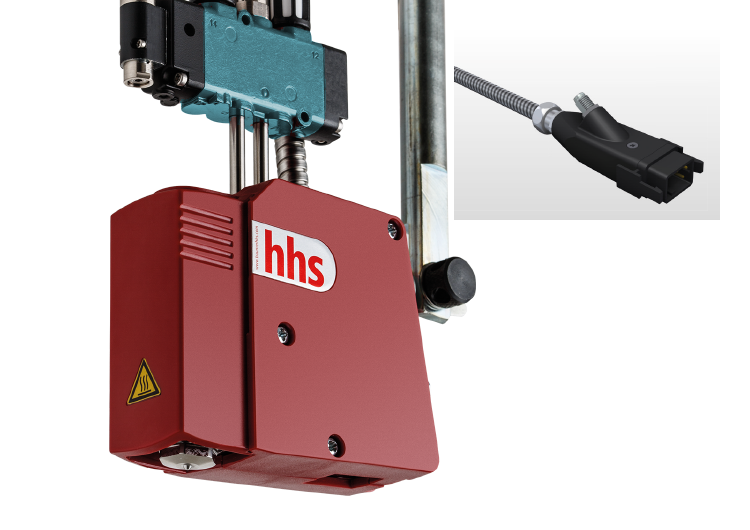
Powerhouse for end-of-line packaging for use with third-party systems
With the aerto go you enjoy the same advantages as with our aerto evo, only here you have the possibility to use existing systems. Due to its compatibility, the aerto go is the perfect start into the technology of Baumer hhs.
- Maximum safety through temperature shut-off
- Highest flexibility in adhesive selection
- Simple control via PLC 24V
- Flexible for dot and line application
- Easy integration due to competition-compatible connections
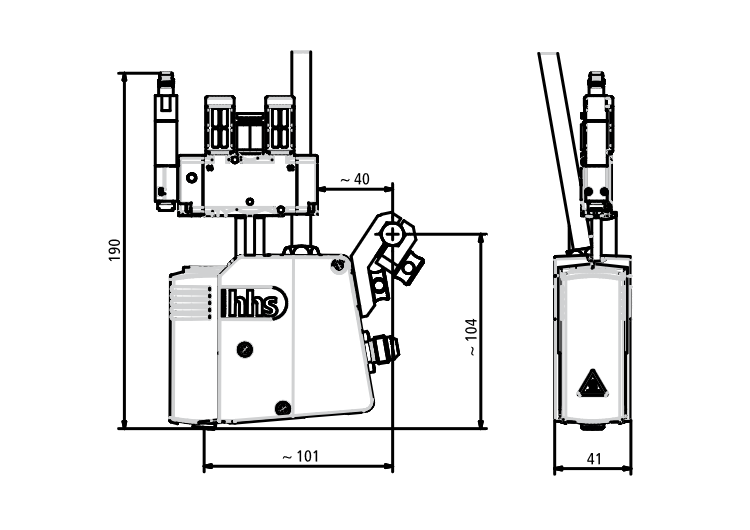
Technical data
Specification | Value | Unit |
---|---|---|
Temperature range | 0-200 | °C |
Temperature monitoring | Ni 120 | |
Switching frequency* | 250 | Hz |
Hose connection | Stecker für den Betrieb an Fremdsystemen | |
Adhesive pressure | 80 | bar |
Adhesive viscosity | max.60.000 | mPa.s |
Noise emission | 82 | dB** |
*Depending on nozzle size, adhesive and pressure **with sound insulation |
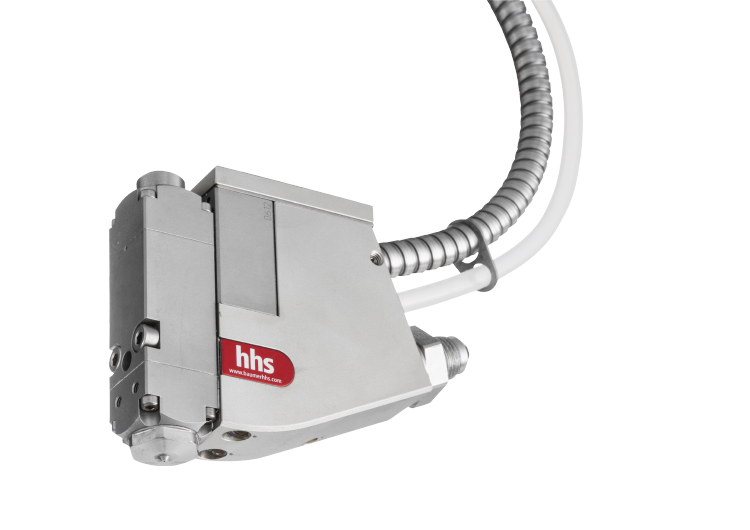
The compact application head
With its integrated pneumatic valve, the HP-500 impresses with its compact design. It can be integrated into the tightest installation spaces and is ideally suited for integration into robotic applications, among others.
- Small installation space
- Great flexibility in the choice of adhesive
- Wide range of applications
- Extremely quiet
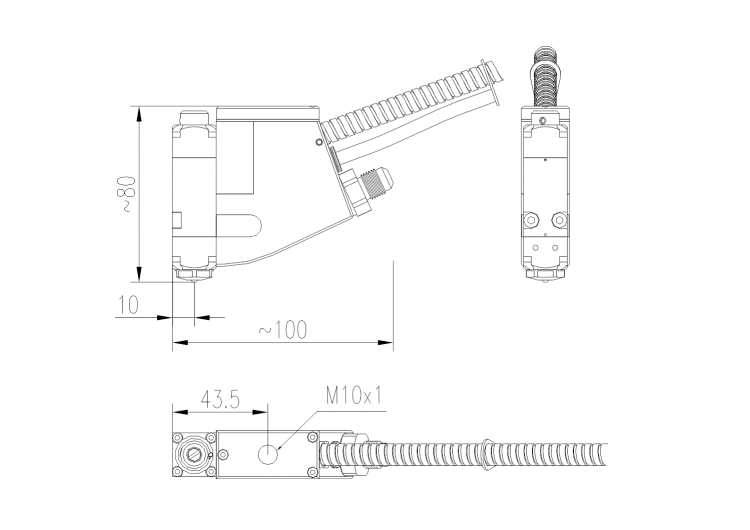
Technical data
Specification | Value | Unit |
---|---|---|
Temperature range | 0-200 | °C |
Temperature monitoring | Pt 100 | |
Switching frequency* | 150 | Hz |
Connection | 9-pole AMP-Plugr | |
Hose connection | 1/2" UNF | |
Adhesive pressure | 80 | bar |
Noise emission | 70 | dB |
*Depending on nozzle size, adhesive and pressure |
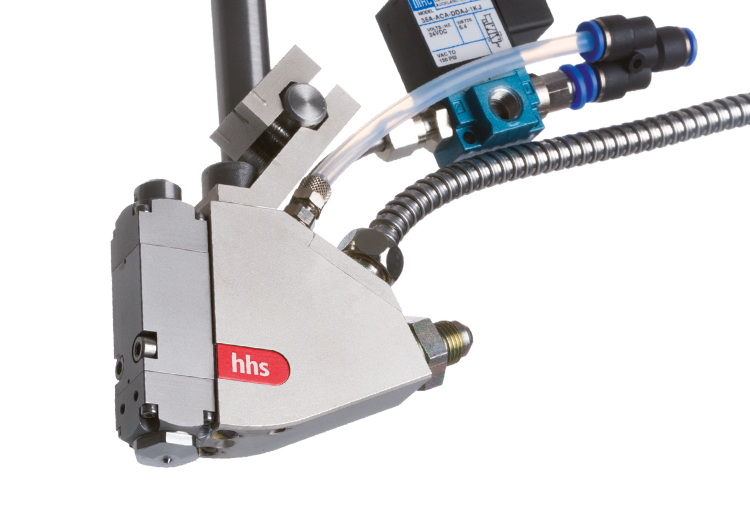
The universal head with power
With the HM-500, Baumer hhs provides an extremely powerful and flexible application head. The HM-500 is suitable for a wide range of applications in many industries.
- Special designs available
- Maximum flexibility
- Maximum flexibility in adhesive selection
- For dot and line application
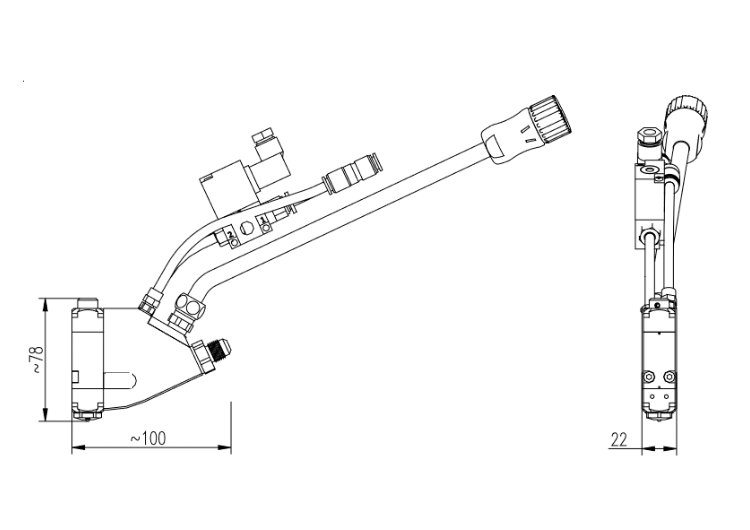
Technical data
Specification | Value | Unit |
---|---|---|
Temperature range | 0-200 | °C |
Temperature monitoring | Pt 100 | |
Switching frequency* | 150 | HZ |
Connection | 15 pole plug | |
Hose connection | 1/2“ UNF | |
Adhesive pressure | 80 | bar |
Adhesive viscosity | max. 60.000 | mPa.s |
Noise emission | 75 | dB |
*Depending on nozzle size, adhesive and pressure |
Xmelt Central adhesive supply Xfeed
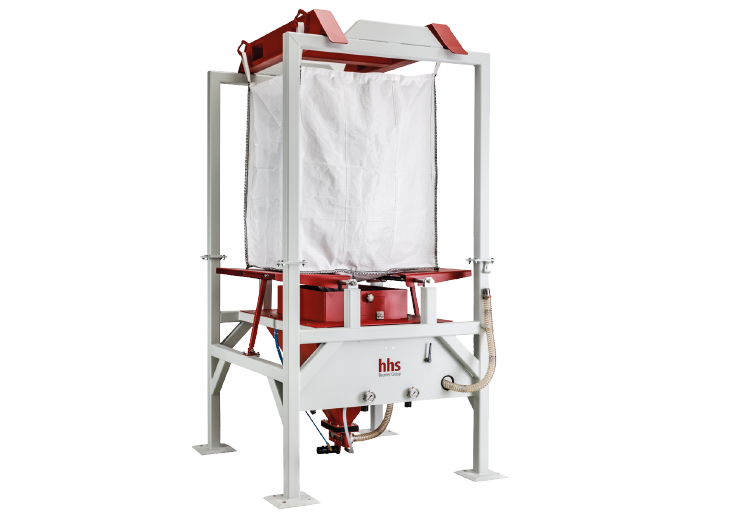
Adhesive supply for large production plants
You want to supply several packaging machines in your production with adhesive? Then the big bag station is exactly the right concept. With a capacity of 1t, you can be sure that all lines are always supplied with the right amount of adhesive.
- No adhesive granules in production
- Maximum cleanliness
- Highest process reliability
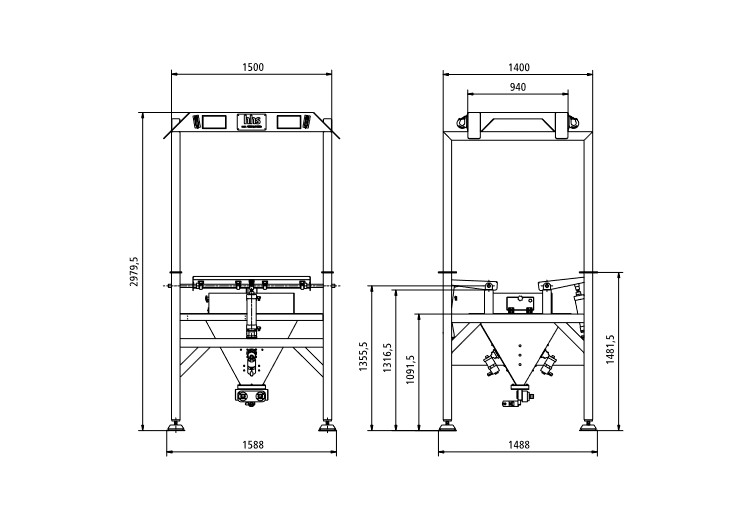
Technical data
Specification | Value | Unit |
---|---|---|
Capacity | 1000 | kg |
Power consumption | 32 | W |
Weight | 641 | kg |
Ambient temperature | 5-40* | C° |
Degree of protection | 54 | IP |
Delivery hose connection | Ø-Innen 40 Ø-Außen 50 | mm |
Air hose connection | Ø-Innen 13 | mm |
Compressed air | 4-6 | bar |
Noise emission | 70,4** | db |
Granulate size | 2-8 +/- 20% | mm |
*Depending on adhesive ** DIN EN ISO 9614-1
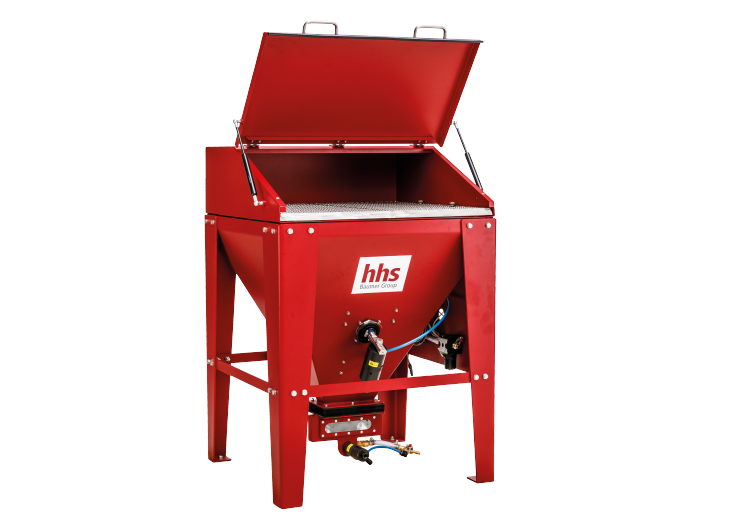
Flexibility in adhesive supply
With a capacity of 125 kg of adhesive granulate, the bag station is the ideal entry into central adhesive supply. This means that there is no longer any need to fill melting equipment.
- No adhesive granulate in production
- Maximum cleanliness
- Highest process reliability
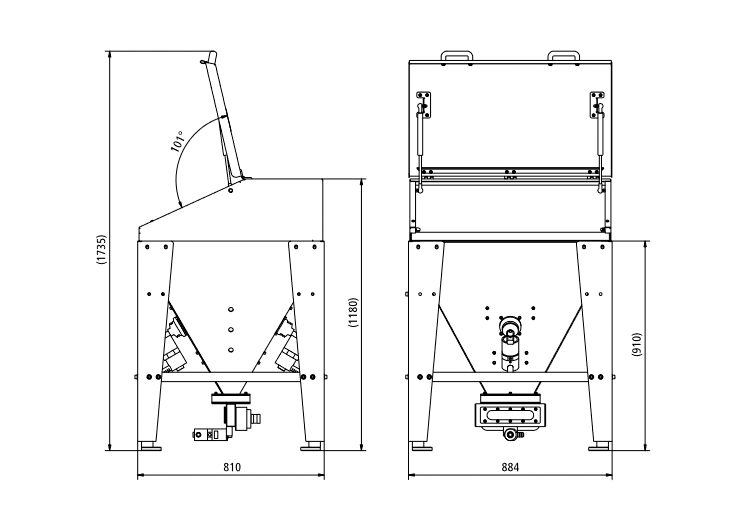
Technical data
Specificaion | Value | Unit |
---|---|---|
Capacity | 125 | kg |
Power consumption | 32 | W |
Weight | 184 | kg |
Ambient temperature | 5-40* | C° |
Degree of protection | 54 | IP |
Delivery hose connection | Ø-inside 40 Ø-outside 50 | mm |
Air-hose connection | Ø-inside 13 | mm |
Compressed air | 4-6 | bar |
Noise emission | 70,4** | db |
Granulate size | 2-8 +/- 20% | mm |
*Depending on adhesive ** DIN EN ISO 9614-1
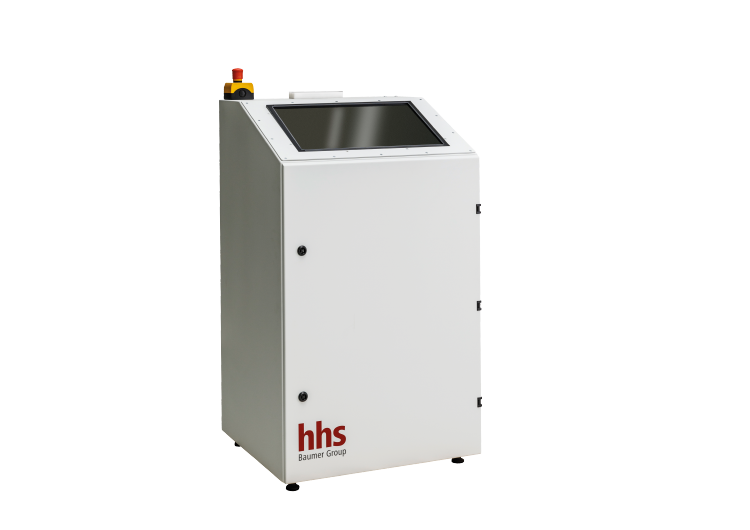
Adhesive distribution to all connected packaging lines according to demand.
With the Xfeed center, you always have an overview of your production. All requirements converge here. The centre distributes the adhesive to all connected lines. Demand-driven and reliable.
The heart of adhesive supply.
- Production always in view
- Dosing tower for delivery volumes from 0.5 l to 10 l
- Automated distribution
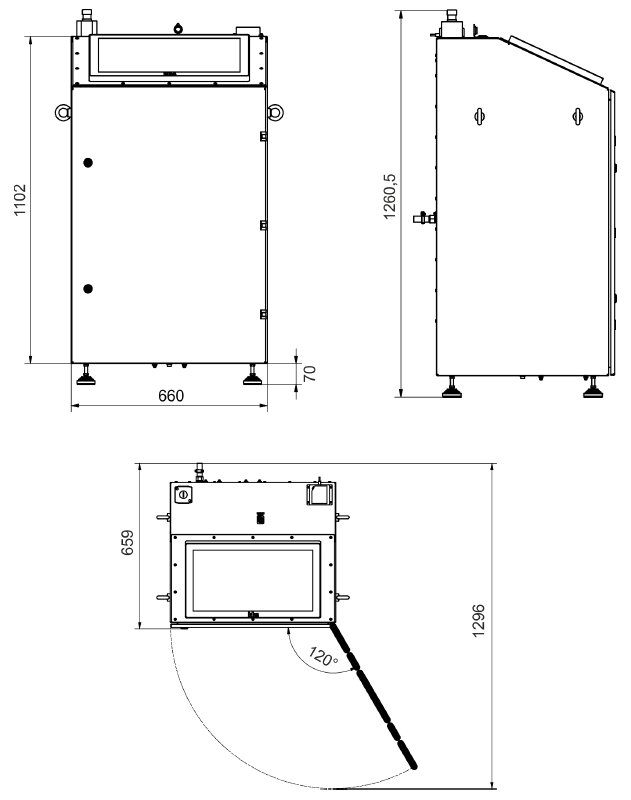
Technical data
Specification | Value | Unit |
---|---|---|
Power consumption | 182 | W |
Weight | 85 | kg |
Delivery volume | 0,5 , 1 , 2 | l |
Ambient temperature | 5-40* | C° |
Degree of protection | 54 | IP |
Delivery hose connection | Ø-Innen 25 Ø-Außen 32 | mm |
Air hose connection | Ø-Innen 19 Ø-Außen 27 | mm |
Compressed air | 2,3-2,7 | bar |
Noise emission | 62,5** | dB |
Granulate size | 2-8 +/- 20% | mm |
*Depending on adhesive, **DIN EN ISO 9614-1
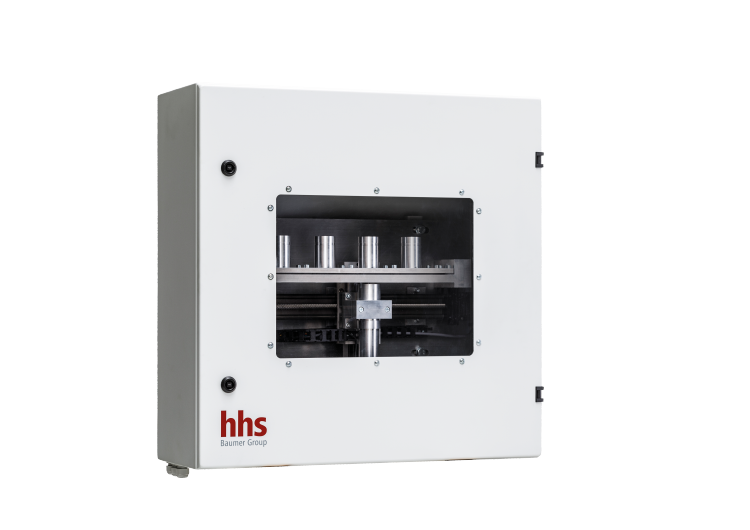
Adhesive distribution
The distributor distributes the adhesive to the connected packaging lines. With its 4 outputs, 4 hot-glue devices can be connected. Should further packaging lines be integrated, the system is expandable
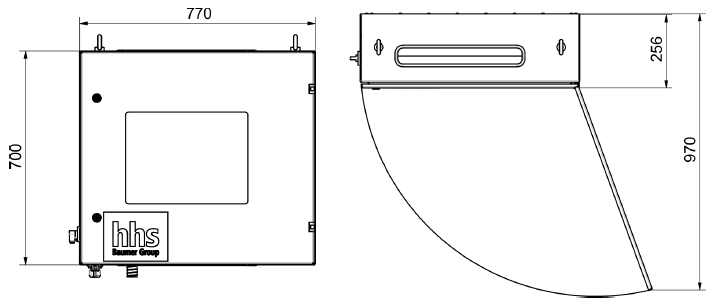
Technical data
Specification | Value | Unit |
---|---|---|
Power consumption | 264 | W |
Weight | 27 | kg |
Ambient temperature | 5-40* | C° |
Degree of protection | 54 | IP |
Delivery hose connection | Ø-Innen 25 Ø-Außen 32 | mm |
Hose connections | 4 | |
Noise emission | 67,3** | dB |
Granulate size | 2-8 +/- 20% | mm |
* Adhesive dependent **DIN EN ISO 9614-1
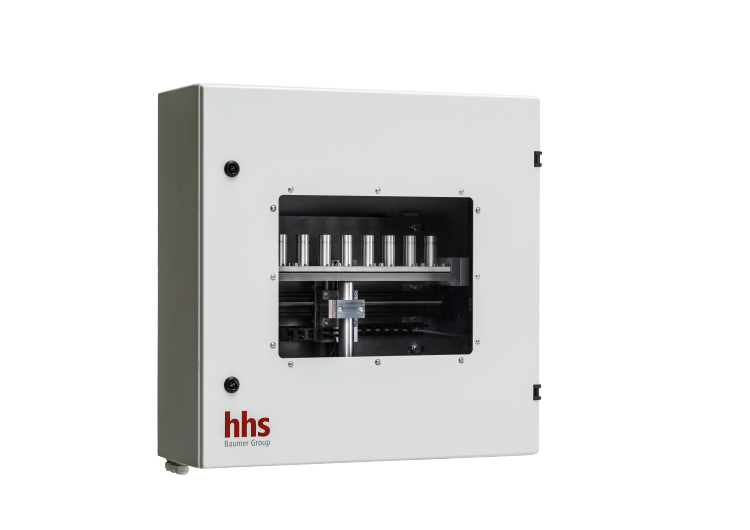
Adhesive distribution
The distributor distributes the adhesive to the connected packaging lines. With its 8 outputs, 8 hot-melt gluers can be connected. If further packaging lines are to be integrated, the system can be expanded.
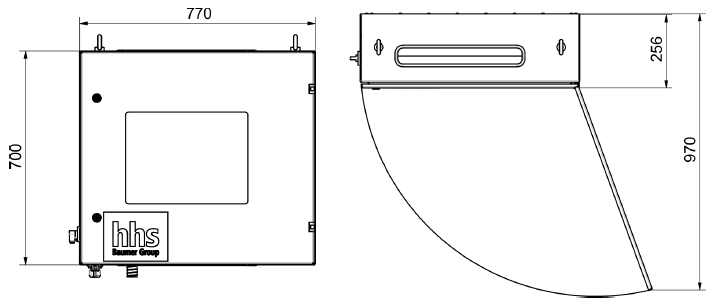
Technical data
Specification | Value | Unit |
---|---|---|
Power consumption | 264 | W |
Weight | 27 | kg |
Ambient temperature | 5-40* | C° |
Degree of protection | 54 | IP |
Delivery hose connection | Ø-Innen 25 Ø-Außen 32 | mm |
Hose connections | 8 | |
Noise emission | 67,3** | dB |
Granulate size | 2-8 +/- 20% | mm |
* Adhesive dependent **DIN EN ISO 9614-1
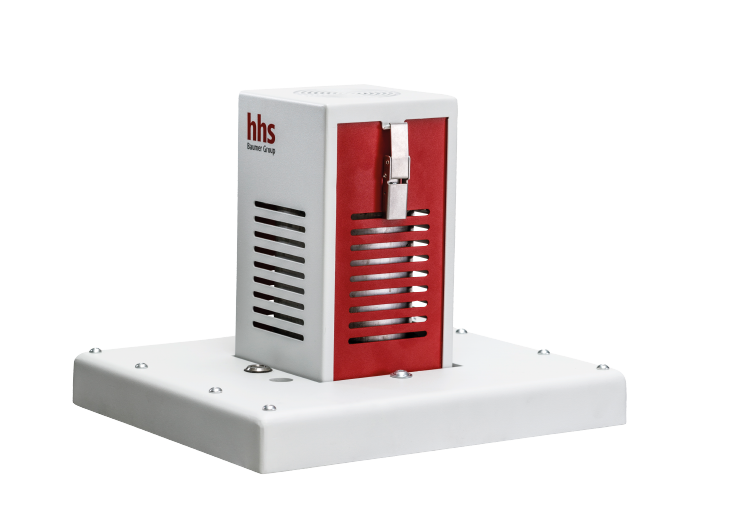
The right system for a wide range of installations
A wide variety of hot-melt devices are often found in a production facility. With the Xfeed filler, you can connect all commercially available melters and fill them with adhesive.
With a capacitive sensor, the filler is always informed about the filling level of the melters and communicates directly with the system when a device needs to be filled.
It couldn't be simpler or safer.
- Always the right fill level
- Maximum occupational safety
- Filling of melters even in the secured area
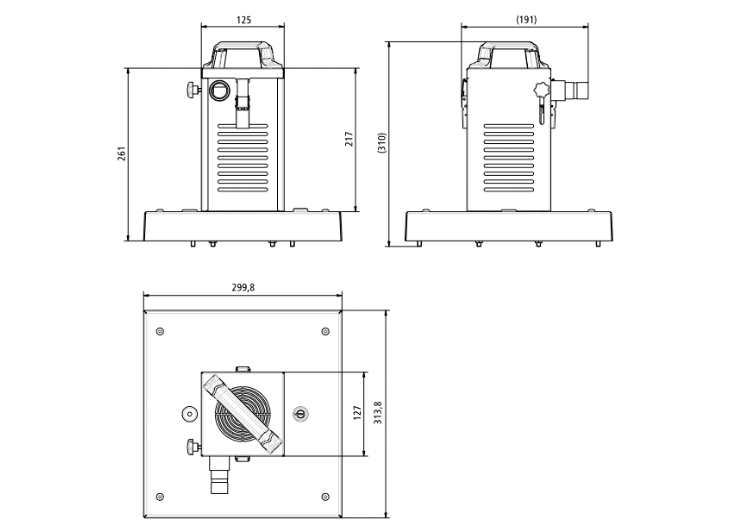
Technical data
Specification | Value | Unit |
---|---|---|
Power consumption | 32 | W |
Weight | 3,5 | kg |
Ambient temperature | 5-40** | C° |
Degree of protection | 54 | IP |
Delivery hose connection | Ø-Innen 25 Ø-Außen 32 | mm |
Noise emission | 72,3 | dB |
Granulate size | 2-8 +/- 20% | mm |
*Depending on adhesive **DIN EN ISO 9614-1
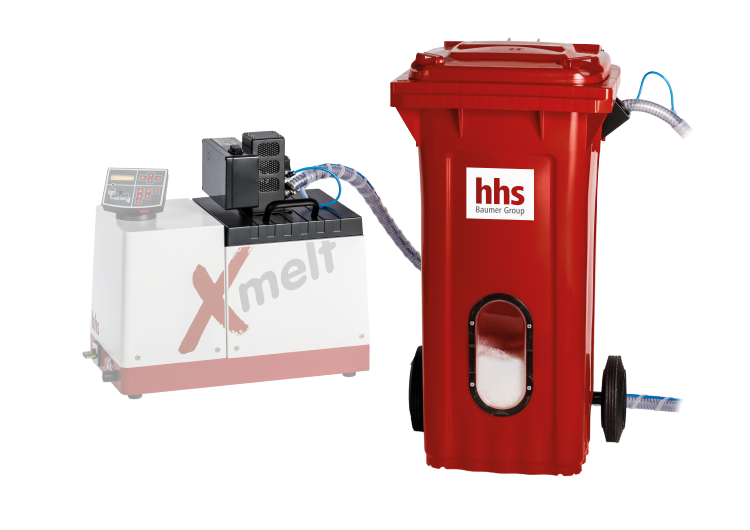
Process-stabilisation and employee protection
In industrial packaging processes, production interruptions and maintenance work are the focus of attention. With the Xfeed single, your melter is always well supplied with adhesive. Production interruptions due to insufficient filling levels are a thing of the past. For maintenance and filling, employees no longer come into contact with heated surfaces and the melters can be placed in the safe area of the packaging machine.
- No contamination of the production environment
- Maximum employee protection
- Highest process reliability and availability
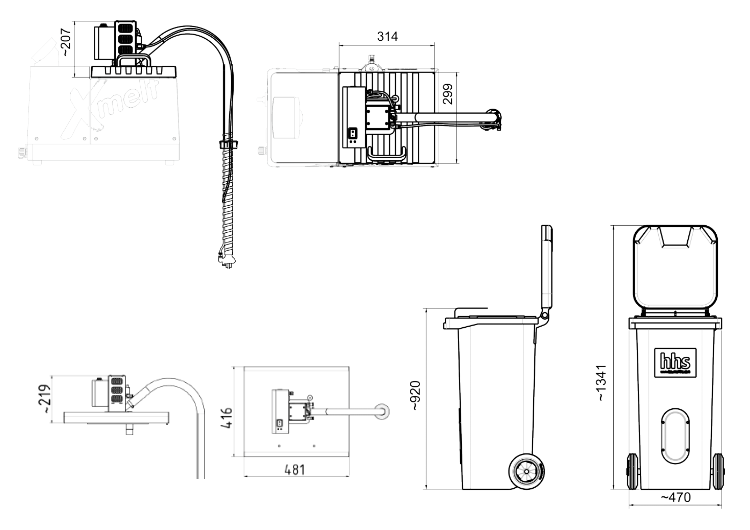
Technical data
Specification | Value | Unit |
---|---|---|
Power consumption | 32 | W |
Weight | 3,5 | kg |
Ambient temperature | 5-40** | C° |
Degree of protection | 54 | IP |
Delivery hose connection | Ø-Innen 25 Ø-Außen 32 | mm |
Noise emission | 72,3 | dB |
Granulate size | 2-8 +/- 20% | mm |
*Depending on adhesive **DIN EN ISO 9614-1
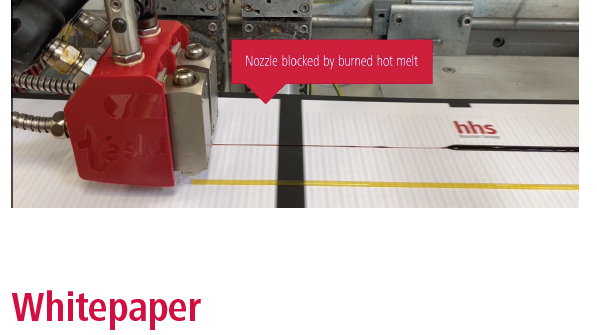
Whitepaper
Xmelt DF
Maximizing Profitability: Preventing Downtime and Disruptions in Hot Melt Application