Volume 03
It starts with sustainability: Product development at Baumer hhs
Introducing Eco Talks
In our Eco Talks series, various people in management positions at Baumer hhs get an opportunity to share their personal insights on the subject of sustainability. In exclusive interviews, they shed light on Baumer hhs's past and ongoing steps to promote sustainability, and they explain exactly how our innovative solutions help customers to minimise their ecological footprint while making production processes more efficient. Eco Talks – Inspiring insight into sustainable innovation and responsibility.
In this episode, Head of Research and Development Marco Ahler talks with Florian Lemke (Digital Content Manager) about sustainability in product development of Baumer hhs.
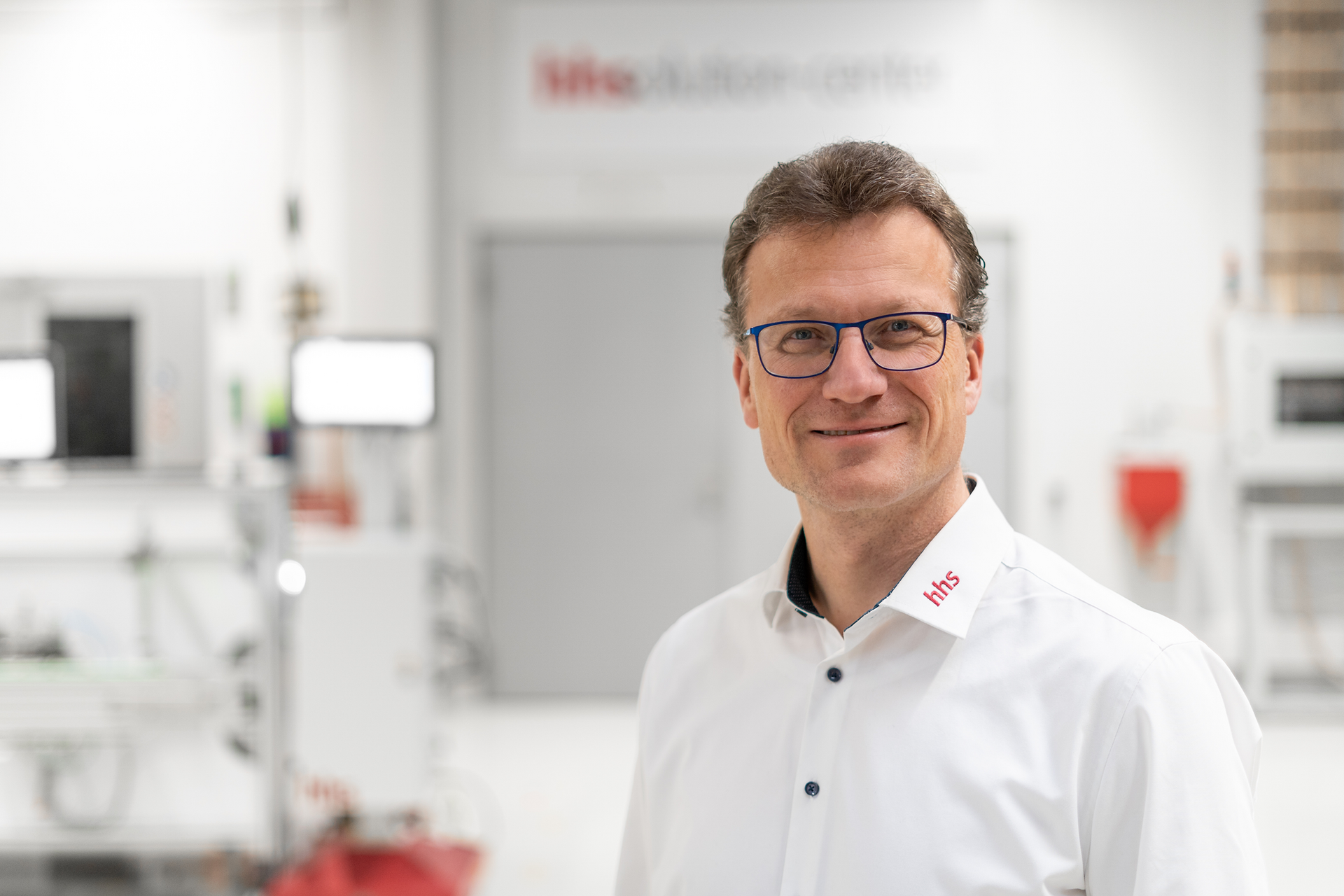
Head of Research & Development
Florian Lemke: Mr. Ahler, sustainability is a hot topic in the industry. How does it affect early product development at Baumer hhs?
Marco Ahler: Conserving resources is a core element of our corporate strategy. We apply principles of resource conservation not only in administrative areas and production, but also in the early phases of product development. Our goal is to supply customers with future-proof products that combine environmental responsibility with high functionality and economic efficiency.
Florian Lemke: How exactly do you apply these principles in such an early phase as product development?
Marco Ahler: The various aspects of sustainability are a decisive criterion from the very beginning, on par with functionality, size, and cost. In designing our products, we concentrate on durability, repairability and recyclability. Our products are engineered to run reliably for many years, to be modular, and to be easily returned to the circular economy as raw materials. At Baumer hhs, it is even a requirement that every new product be more resource-efficient than its predecessor. This ensures that we continuously make progress and improve our environmental footprint.
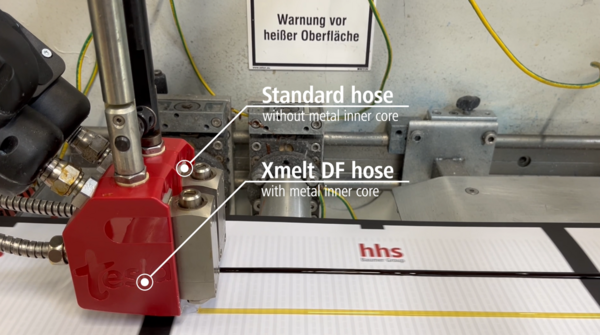
Florian Lemke: How do you verify that these principles are followed systematically?
Marco Ahler: As part of our development process, we have established a proven environmental management system. It helps us to objectively quantify various criteria and balance them against other relevant factors such as cost or performance. Similar to a total cost of ownership (TCO) analysis, we look at environmental efficiency across the entire life cycle of our products.
Florian Lemke: Can you give a concrete example of the decisions involved?
Marco Ahler: Gladly. A classic example is the decision to use metal or plastic housings. A metal housing may have a higher initial cost, but it is offset by metal’s better repairability and better recycling options. Another example is premium insulation materials for our hot melt units: The higher initial cost of better thermal insulation is offset over the years by the tremendous savings on energy.
Florian Lemke: Saving energy is another way to improve eco-friendliness. What specific steps are you taking in this area?
Marco Ahler: We continuously optimise our adhesive melting technologies, improve the insulation of our hot melt units and use intelligent temperature controllers. For example, our systems detect when a maximum melt rate is unnecessary, and adjust the temperature accordingly. This is one way we reduce energy consumption.
Florian Lemke: Adhesive consumption is another key factor in addition to energy use. How do you approach it?
Marco Ahler: Reducing adhesive consumption is in fact the greatest lever we have for conserving resources. Using less adhesive means using less material, but also less energy, because not as much adhesive needs to be melted. We are focussing on innovative dotting and stitching technologies that allow our systems to apply smaller volumes of adhesive with absolute precision. We also are promoting the use of cold/low-melt adhesives that can be processed with lower heat input.
Florian Lemke: Another issue is reducing production waste. What steps is Baumer hhs taking here?
Marco Ahler: Our quality assurance systems detect errors very early on, meaning that defective products don’t even make it to the production process. They are detected and automatically ejected. If an error occurs repeatedly, the machine can even be stopped. That reduces material waste and saves the energy otherwise consumed for production.
Florian Lemke: A common problem of hot melt application is charring of the adhesive. Does Baumer hhs have any innovations to counteract it?
Marco Ahler: Yes we do. Our new DF hot melt hoses virtually rule out any adhesive char. Thanks to the metal core, the adhesive inside does not come into contact with oxygen and cannot char. This solution prevents clogging of the filters and nozzles, which in turn reduces machine downtime. The result is a significant increase in process reliability. Not to mention the fact that the hoses significantly reduce maintenance, because they generate less residue and guarantee that the quality of the adhesive remains constant over prolonged periods. This technology offers major advantages to the packaging industry, where interruptions in production can generate high costs.
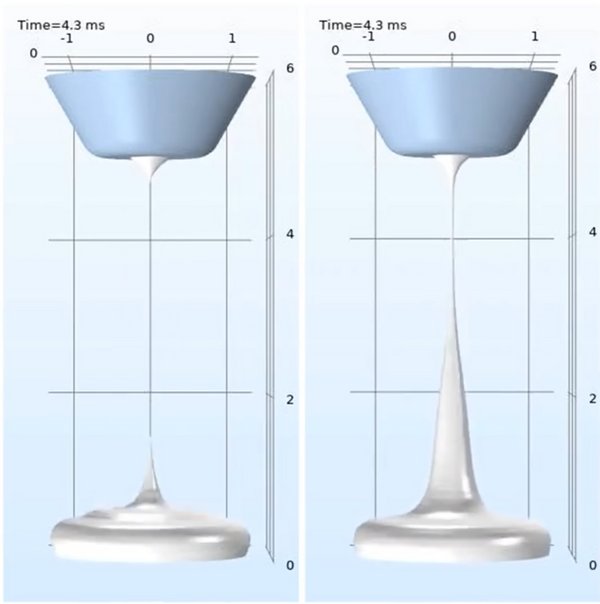
Florian Lemke: Are there other aspects of sustainability that often get overlooked?
Marco Ahler: The ease-of-maintenance of our systems is a critical factor. With modular designs and easily replaceable components, we can minimise the time and effort required for repairs. We only have to replace individual parts, not the whole device, meaning we conserve resources and cut costs. We are also working on new ideas for re-using components to further optimise material recycling.
Florian Lemke: Do you have any other innovations that support your strategy for conserving resources?
Marco Ahler: Our Development department constantly tests our products and systems to make them even more efficient and eco-friendly. We analyse how to further cut energy consumption, use materials more efficiently and optimise production processes. Our focus is on continuously finding new ways to unite environmental responsibility with high performance. We are also expanding digitalisation. The goal here is to improve the efficiency of production processes using data-based solutions. For instance, digital assistants help to automatically identify energy saving potentials and optimize operating parameters. Another important tool we use in development is the simulation software COMSOL. With it, we can analyse physical processes in detail and optimise them even before building a prototype. Simulation helps us to reduce material use in the development phase and verify that our products function properly under real conditions. It enables us to develop more resource-efficient designs and further boost the efficiency of our systems.
Florian Lemke: One last question: How would you describe the future of sustainability at Baumer hhs?
Marco Ahler: Responsible resource management is a ongoing commitment for us. We will continue to develop innovative technologies, implement smart designs and establish energy-efficient processes. Our goal is to minimise our environmental footprint, while helping our customers to achieve their own environmental objectives. By taking all of these steps, we make sure that our products deliver maximum quality and efficiency, meet the challenges of the future and conserve resources.