Precise Folding, Stable Packaging: Why Dimensional Deviations Are Not Just a Nuisance, But a Problem
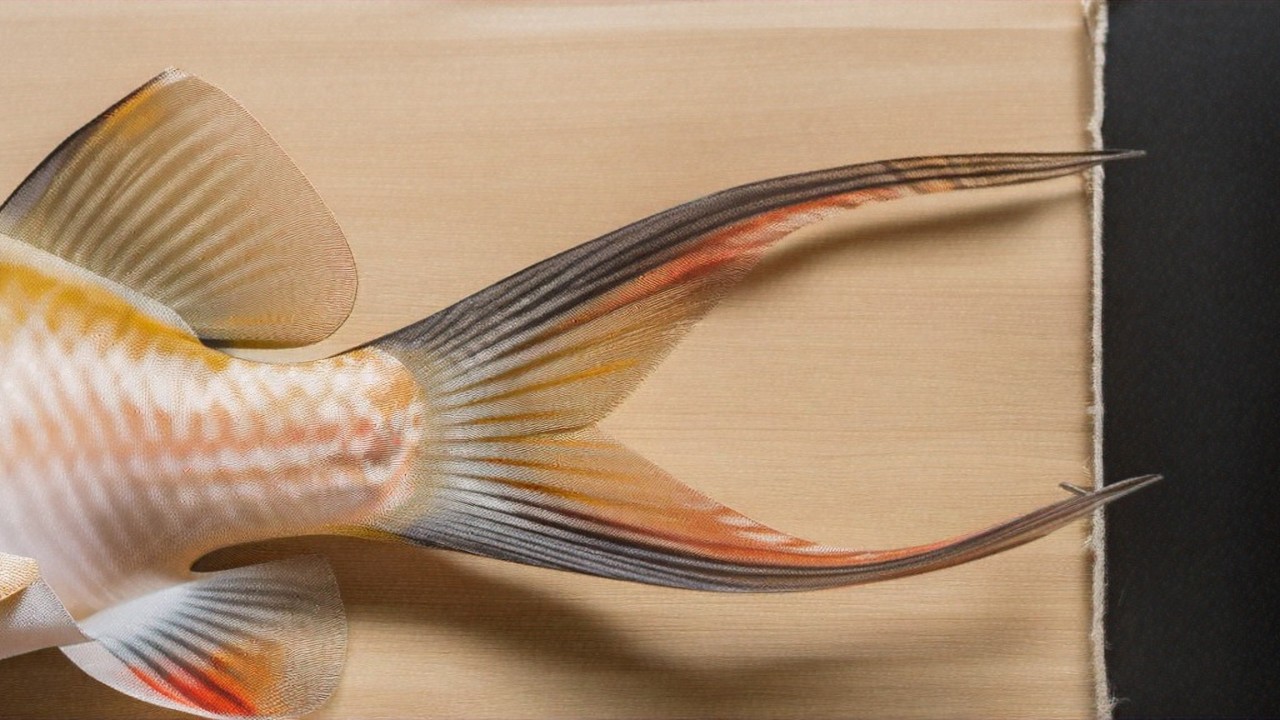
Economic and Ecological Sustainability: Key to the Long-Term Success of Corrugated Packaging Manufacturers
Economic and ecological sustainability are not just buzzwords but essential for the long-term success of corrugated packaging manufacturers. The potential for creating sustainable value is vast and often remains untapped. The goal is to increase ecological and economic value in a focused manner. This article presents practical approaches for companies to enhance their competitiveness, emphasizing that environmental sustainability is not a burden but a strategic move that can generate significant economic benefits.
Reducing waste, overproduction, and quality defects in packaging is a key strategy for achieving more sustainable and efficient packaging production. Preventing product recalls related to inadequate packaging or quality issues is equally important. By optimizing manufacturing processes, utilizing high-quality production tools, and improving production control, companies can use resources more efficiently, lower costs, and strengthen their competitiveness.
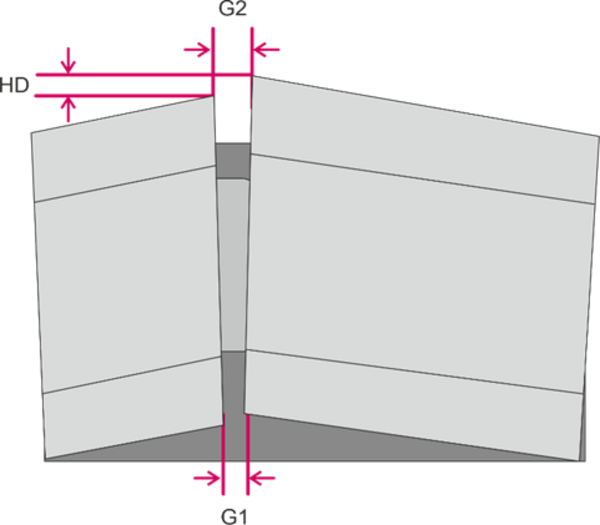
Precise Folding, Stable Packaging: Why Dimensional Deviations Are Not Just a Nuisance, But a Problem
Dimensional deviations occur when the edges of a folded box or blank do not align evenly, causing them to diverge and create a fishtail shape—hence the term "fish-tailing." These deviations negatively impact the quality and stability of packaging, leading to problems during further processing and sealing. They are a common source of product complaints in automated erecting processes.
Sorting out affected packaging can be more than just uneconomical and resource-intensive. It can lead to significant financial losses and environmental harm, as all resources used are wasted without the packaging being utilized. This underscores the need for efficient and effective solutions to prevent such losses.
Moreover, dimensional deviations compromise stability during palletization. Open gaps due to uneven panel alignment can allow contaminants or pests to enter, jeopardizing product safety.
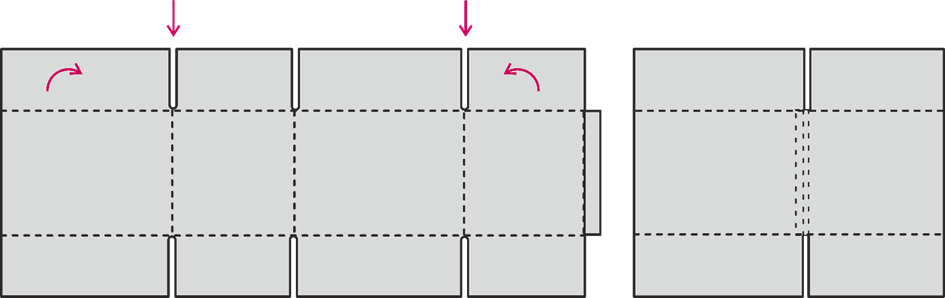
Folding corrugated board
Scoring or perforating corrugated boards is a crucial process that enables precise folding along defined lines. In this process, the board is pressed into a grooved die using a stamp, which alters its material structure. Cutting and scoring tools apply significant force to penetrate the material, reducing its bending stiffness and allowing for easier folding along the scored lines.
During scoring, high shear forces act on the layers of the material, creating both vertical and horizontal stresses. This can damage the liner layers, often resulting in issues that only become apparent during folding. A common problem is the unintended weakening of the area surrounding the score line. Consequently, the material may fold away from the intended line, leading to inaccuracies in the gap dimensions at the manufacturer's joint.
The manufacturer's joint is the connection point of a corrugated box where the two ends of the blank are joined, typically by gluing. Inaccuracies in scoring and folding can cause misalignment at this joint, which compromises the stability and dimensional accuracy of the final packaging.
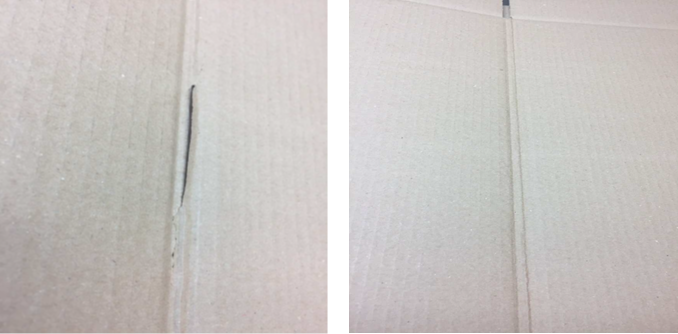
Criteria for Precise and Defect-Free Folding
From the perspective of a corrugated packaging manufacturer, the following criteria are essential for minimizing complaint costs. The importance of each criterion may vary depending on the target market and packaging application [1],[2]:
Material Integrity: The corrugated board should not tear during scoring.
Precise Folding: Unintended folding should not occur in adjacent flutes when scoring parallel to the flute. The bending point must be clearly defined.
Score Stability: There should be no tearing when folding at a 180° angle along the score line. This means the board should be able to fold back on itself without any damage or tearing, ensuring a smooth and stable fold.
Dimensional Accuracy: The deviation in fold straightness should not exceed half the thickness of the corrugated board.
Bending Stiffness: There should be a sufficient reduction in bending stiffness along the folding point.
Influence of Score Position on Folding Quality in Parallel Flute Direction
Research [2] indicates that scoring perpendicular to the flute direction is generally less critical, allowing for deeper penetration of the scoring tool. In contrast, scoring parallel to the flute direction is much more sensitive and is significantly influenced by its position in relation to the flute.
Tests conducted on 180 single- and double-wall samples under standard climate conditions (EN ISO 187:2023-02) yielded the following insights: the scoring alignment was adjusted in 30° increments relative to the flute direction. All orientations, except for the parallel score, produced nearly identical results. However, when scoring parallel to the flute, the position of the scoring wheel in relation to the flute becomes crucial. A deeper score can be achieved without tearing the liner if the scoring wheel is precisely positioned at the peak of the flute. Conversely, scoring in the valley between two flutes significantly increases the risk of tearing.
The tests revealed that the least favorable position for the scoring wheel is about 20% of the distance between two flutes. Additionally, images from the Papiertechnische Stiftung (PTS) indicate that increased shear forces can lead to deformation and compression in adjacent areas when scoring either in the flute valley or on the flute peak. As a result, it is not always guaranteed that folding will occur along the predefined folding line.
Lateral and uneven force distribution can result in locally varying gap dimensions (GAP). Factors such as flute spacing, the number of layers, paper type, and residual moisture significantly influence these deviations. While manufacturers often recommend material-dependent scoring wheels, extensive retooling is typically avoided.
![Figure 4: Scoring in the flute valley[1] Figure 4: Scoring in the flute valley[1]](/fileadmin/user_upload/1741635582104.png)
![Figure 5: Scoring at the flute top [1] Figure 5: Scoring at the flute top [1]](/fileadmin/user_upload/1741635625170.png)
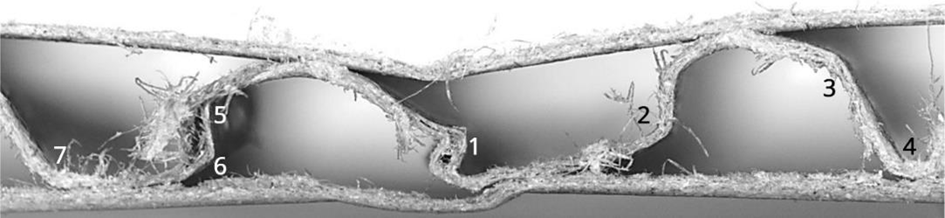
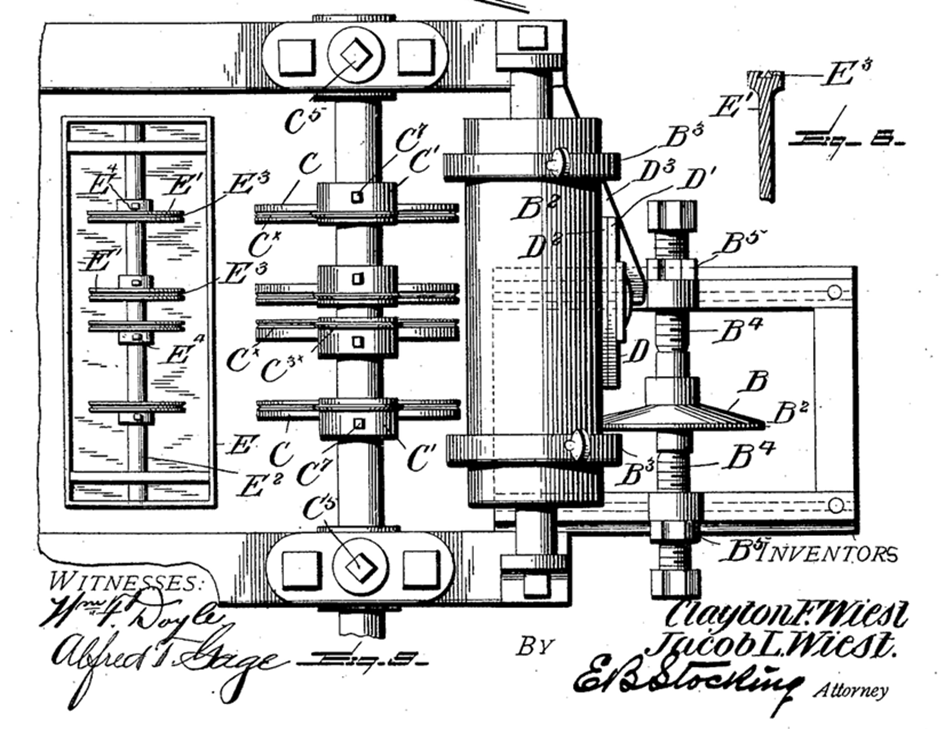
Water Scoring: Where Tradition Meets Modern High-Performance Technology
Creasing technology was still evolving at the turn of the 20th century. However, as production processes were quite inefficient at that time, producers needed to operate efficiently and minimize material waste.
Water was applied to the creasing lines both before and after the creasing process to enhance the scoring and reduce bending stiffness. This long-forgotten technique, known as "water scoring," is experiencing a revival. Water scoring involves precisely applying a fine line of liquid through nozzles that can be controlled to ensure the right amount of moisture is applied. This technique significantly improves the folding quality of corrugated boards, reduces the risk of tearing, and ensures accurate folding.
Customers of Baumer hhs in the corrugated board packaging industry report that water scoring ensures folds occur exactly at the intended points. This precision minimizes gap deviations and results in excellent packaging dimensions. It's important that the area around the creasing line is not oversaturated, allowing moisture to penetrate the material quickly.
While rapid moisture penetration was once considered less important, it has become essential today. Modern inliners and multipoint gluers can operate at speeds of up to 450 m/min. Consequently, the water scoring process must function reliably under these high-performance conditions. This reliability is crucial for reducing complaint costs, particularly for packaging that presents challenges during folding.
The main advantage of water scoring is its ability to significantly reduce complaint rates and the number of rejected products during production. This not only lowers economic and ecological costs but also enhances customer satisfaction. Furthermore, preventing a single recall due to issues—such as those arising from assembly problems—can justify the initial investment in this technology.
For further information, please refer to the download link provided.
Waterscoring_brochure_EN_LR.pdf
Thomas Walther - Baumer hhs Gmbh
[1] Anke Nikowski, Katharina Roeber, Benjamin Hiller, Franziska Schlimpert,Prof. Dr.-Ing. Eugen Herzau, RILLEN VON WELLPAPPE FEHLERANALYSE UND -VERMEIDUNG UNTER VERWENDUNG GEZIELTER MATERIALUNTERSUCHUNGEN UND HERLEITUNG VON ZUSAMMENHÄNGEN ZU QUALITÄTSPARAMETERN, Wellpappenachrichten 1/2023, Link.
Anke Nikowski, Rillen von Wellpappe, PTS Wellpappensymposium, 8.5.2024
[2] Nica, W. & Chalmet, R. & Roman, J. & Juwet, M.. (2020). Inline corrugated board creasing. Procedia Manufacturing. 51. 501-504. 10.1016/j.promfg.2020.10.070.
#Corrugated #folding #wellpappe #packaging #packagingindustry